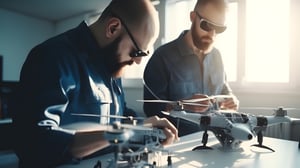
25 Emerging Innovations in Aviation Maintenance
Celebrate our remarkable 25-year journey in building purpose-built aviation solutions by delving into these exciting new concepts and cutting-edge technologies that may be coming in the next 25 years.
TABLE OF CONTENTS
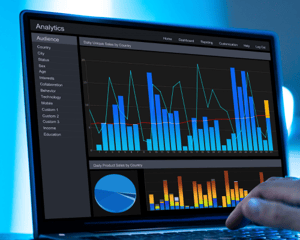
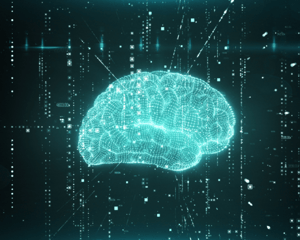
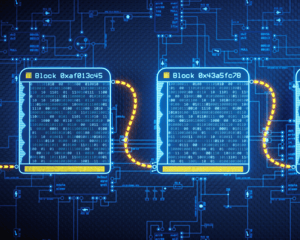
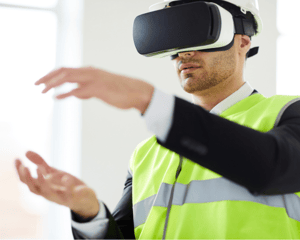
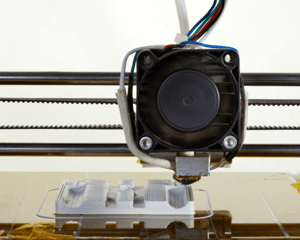
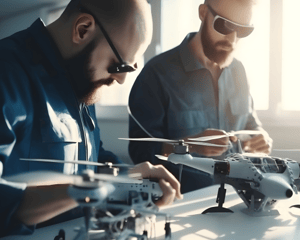
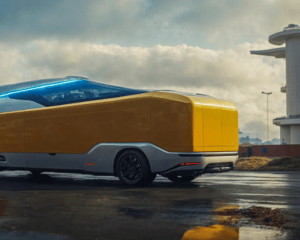
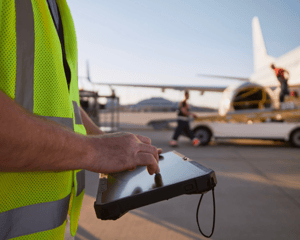
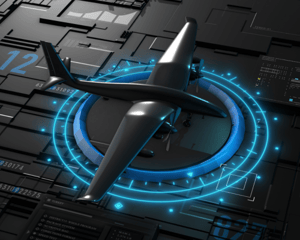
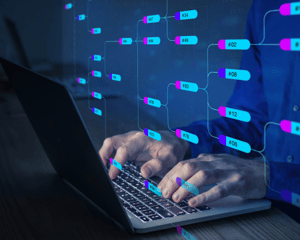
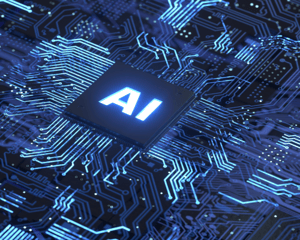
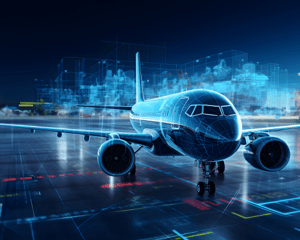
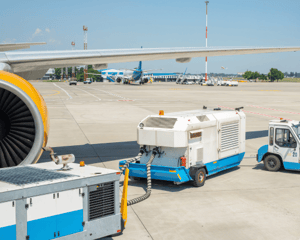
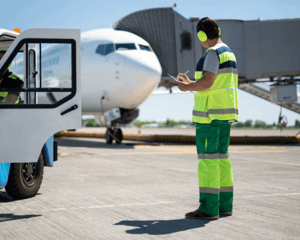
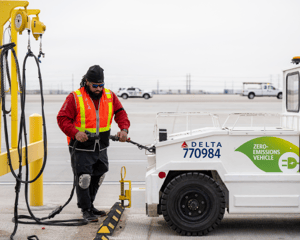
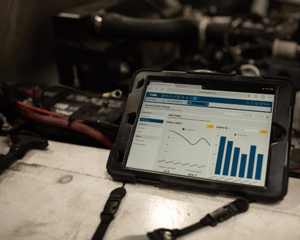
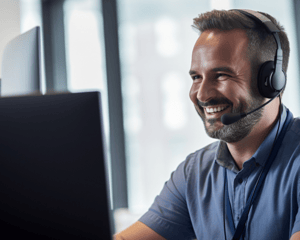
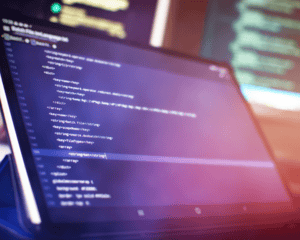
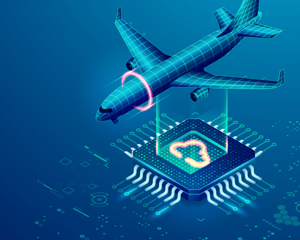
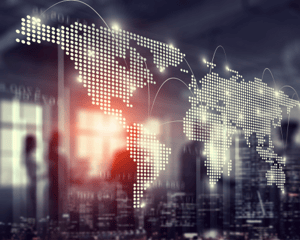
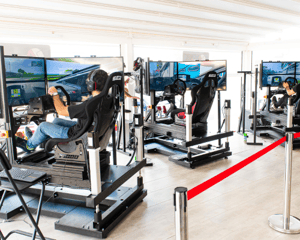
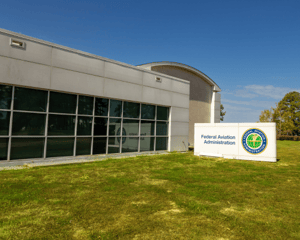
1. The Rise of Predictive Maintenance
In the ever-evolving landscape of aviation, safety and efficiency are paramount. From the towering giants of the sky to the intricate ground support equipment (GSE) that ensures smooth operations on the ground, maintenance plays a crucial role in keeping the industry soaring. Traditionally, aircraft and ground support equipment maintenance have relied heavily on reactive approaches, where issues are addressed after they've occurred, sometimes leading to costly downtime and safety concerns. However, a paradigm shift is underway. Predictive maintenance, propelled by advanced analytics and machine learning, is poised to revolutionize the field, ushering in an era where potential problems are anticipated and resolved before they even arise.
Gone are the days of waiting for a breakdown to occur before taking action. With predictive maintenance, aircraft and ground support equipment communicate their health status in real-time, empowering maintenance crews with invaluable insights. Imagine a scenario where an aircraft's engine signals an impending issue well before it reaches a critical stage. Maintenance teams can then proactively schedule repairs during routine maintenance intervals, minimizing disruption to flight schedules and preventing costly repairs down the line. Similarly, GSE can alert technicians to worn-out components or potential failures, ensuring seamless ground operations and avoiding unexpected downtime.
At the heart of predictive maintenance lies advanced analytics and machine learning algorithms. These technologies analyze vast amounts of data collected from sensors embedded within aircraft and GSE, along with historical maintenance records, to identify patterns and predict potential failures with unprecedented accuracy. By leveraging these insights, maintenance teams can prioritize tasks, optimize resource allocation, and ultimately enhance overall operational efficiency. Moreover, as these algorithms continue to learn from new data inputs, their predictive capabilities will only improve over time, enabling even more proactive maintenance strategies.
One of the key advantages of predictive maintenance is its ability to transition maintenance activities from a reactive to a proactive stance. Instead of merely reacting to problems as they occur, maintenance crews can now take proactive measures to prevent them altogether. For instance, rather than waiting for a hydraulic system to fail, sensors can detect subtle changes in pressure or temperature, indicating potential issues long before they manifest. By addressing these early warnings, maintenance teams can perform targeted interventions, such as replacing worn-out components or adjusting operating parameters, effectively mitigating the risk of failure and extending the lifespan of critical assets.
Furthermore, predictive maintenance offers significant cost savings compared to traditional reactive approaches. By preventing unplanned downtime and minimizing the need for costly emergency repairs, airlines and ground handling companies can reduce maintenance-related expenses while maximizing asset utilization. Additionally, predictive maintenance enables more efficient inventory management by accurately forecasting spare parts requirements based on anticipated maintenance needs. This results in reduced inventory carrying costs and eliminates the need for excess stockpiling, further optimizing operational expenditure.
The implementation of predictive maintenance also fosters a culture of continuous improvement within maintenance operations. By continuously monitoring equipment performance and analyzing maintenance outcomes, organizations can identify opportunities for optimization and refinement. Insights gleaned from predictive maintenance data can inform decision-making processes, driving iterative improvements in maintenance procedures, equipment design, and operational workflows. Moreover, by fostering collaboration between maintenance teams, data analysts, and engineers, organizations can harness collective expertise to develop innovative solutions and stay at the forefront of technological advancements. However, the transition to predictive maintenance is not without its challenges. One of the primary obstacles is the integration of disparate data sources and legacy systems across different aircraft and GSE models. Standardizing data formats and protocols to enable seamless communication and interoperability remains a significant hurdle. Additionally, ensuring data accuracy and reliability is crucial, as erroneous or incomplete data can lead to false alarms or missed opportunities for intervention. Therefore, robust data governance frameworks and quality assurance mechanisms are essential to uphold the integrity of predictive maintenance systems.
Furthermore, the successful implementation of predictive maintenance relies heavily on skilled personnel capable of interpreting data insights and taking appropriate action. Training maintenance crews in data analytics and machine learning techniques is imperative to maximize the effectiveness of predictive maintenance programs. Moreover, fostering a culture of innovation and continuous learning within maintenance organizations is essential to adapt to evolving technologies and embrace new methodologies.
Despite these challenges, the benefits of predictive maintenance far outweigh the initial hurdles. By harnessing the power of advanced analytics and machine learning, aviation maintenance is poised for a transformational leap forward. The days of reactive maintenance are numbered, making way for a future where aircraft and ground support equipment communicate their health status in real-time, enabling maintenance crews to address issues before they escalate. With predictive maintenance at the helm, the skies will be safer, operations more efficient, and the industry better poised for the challenges of tomorrow.
2. The AI Revolution in Diagnostics
In the intricate dance of aviation maintenance, troubleshooting complex issues has long been a challenge. From intricate aircraft systems to the labyrinthine network of ground support equipment (GSE), pinpointing and resolving issues swiftly is imperative for safety and operational efficiency. However, a new era is dawning, one where Artificial Intelligence (AI) takes center stage in diagnostics. By harnessing the power of AI-driven algorithms, aviation maintenance is poised to undergo a profound transformation, ushering in an era of unprecedented efficiency and accuracy in issue resolution.
At the heart of this revolution is the ability of AI algorithms to sift through vast amounts of data with unparalleled speed and precision. Modern aircraft and ground support equipment are equipped with a myriad of sensors that constantly monitor various parameters such as temperature, pressure, vibration, and more. These sensors generate a deluge of data, providing a wealth of information about the health and performance of critical systems. However, extracting actionable insights from this data can be akin to finding a needle in a haystack – a daunting task that often requires significant time and expertise.
This is where AI-driven diagnostics shine. By leveraging advanced machine learning algorithms, AI systems can analyze sensor data in real-time, detecting patterns, anomalies, and correlations that may elude human observers. These algorithms can identify subtle deviations from normal operating parameters, flagging potential issues long before they escalate into full-blown failures. Moreover, as AI systems continuously learn from new data inputs and refine their models over time, their diagnostic capabilities become increasingly sophisticated and accurate.
Imagine a scenario where an aircraft's engine begins exhibiting unusual vibrations during flight. In the past, diagnosing the underlying cause of this issue might have involved a time-consuming process of trial and error, requiring extensive manual inspections and tests. However, with AI-driven diagnostics, the process becomes streamlined and efficient. By analyzing data from onboard sensors in real-time, AI algorithms can pinpoint the root cause of the vibrations with remarkable accuracy, whether it be a faulty component, a misalignment, or some other issue. Maintenance crews can then take targeted corrective action, minimizing downtime and ensuring the safety of both passengers and crew.
The benefits of AI-driven diagnostics extend beyond the realm of aircraft to encompass ground support equipment as well. From baggage handling systems to aircraft tugs, GSE plays a critical role in ensuring smooth operations on the ground. However, like their airborne counterparts, GSE is susceptible to malfunctions and failures that can disrupt operations and incur costly delays. By integrating AI-driven diagnostics into GSE maintenance workflows, operators can proactively identify and address issues before they impact operations, maximizing equipment uptime and minimizing disruptions.
One of the key advantages of AI-driven diagnostics is their ability to automate and augment the expertise of maintenance personnel. While seasoned technicians possess invaluable knowledge and experience, they are ultimately limited by human cognitive capacity and time constraints. AI algorithms, on the other hand, can process and analyze data at speeds far beyond human capability, rapidly identifying trends and anomalies that may go unnoticed by human observers. This enables maintenance crews to focus their efforts more efficiently, directing their attention to areas that require human intervention while delegating routine monitoring and analysis tasks to AI systems.
Moreover, AI-driven diagnostics have the potential to revolutionize predictive maintenance strategies. By continuously monitoring equipment performance and health status, AI algorithms can forecast potential failures and recommend proactive maintenance actions to prevent them. This shift from reactive to proactive maintenance not only reduces the risk of unplanned downtime but also extends the lifespan of critical assets, ultimately leading to cost savings and operational efficiency gains.
However, the widespread adoption of AI-driven diagnostics in aviation maintenance is not without its challenges. One of the primary obstacles is the need for robust data infrastructure and integration capabilities. Ensuring seamless communication and interoperability between disparate data sources and systems is essential for AI algorithms to access the data they need to perform accurate diagnostics. Additionally, concerns regarding data privacy, security, and regulatory compliance must be addressed to mitigate potential risks associated with the use of AI in sensitive aviation operations.
Furthermore, the successful implementation of AI-driven diagnostics requires a workforce that is equipped with the necessary skills and expertise to leverage these technologies effectively. Training maintenance personnel in data analytics, machine learning, and AI technologies is essential to maximize the benefits of AI-driven diagnostics and ensure smooth integration into existing maintenance workflows. Moreover, fostering a culture of innovation and continuous learning within maintenance organizations is crucial to facilitate the adoption of new technologies and methodologies.
In conclusion, the emergence of AI-driven diagnostics represents a paradigm shift in aviation maintenance, offering unprecedented efficiency, accuracy, and insight into complex issue resolution. By harnessing the power of AI algorithms to analyze vast amounts of data from sensors on both aircraft and ground support equipment, maintenance crews can identify and address issues with remarkable speed and precision. Moreover, AI-driven diagnostics pave the way for proactive maintenance strategies that prevent failures before they occur, leading to cost savings and operational efficiency gains. While challenges remain, the potential benefits of AI-driven diagnostics are too significant to ignore, making them the linchpin of future aviation maintenance practices.
3. The Power of Blockchain for Transparent Record-Keeping
In the intricate world of aviation maintenance, precision, accuracy, and transparency are non-negotiable. Every maintenance action, whether it's on an aircraft or ground support equipment (GSE), must be meticulously documented to ensure compliance with regulatory standards and to guarantee the safety of passengers and personnel. However, traditional record-keeping methods often fall short, plagued by issues such as data tampering, lack of transparency, and inefficiency. Enter blockchain technology – a revolutionary solution poised to transform record-keeping in the aviation maintenance industry. By providing a tamper-proof and transparent ledger system, blockchain promises to streamline maintenance logs, enhance compliance with regulations, and foster trust in the integrity of maintenance records.
At its core, blockchain is a decentralized digital ledger that records transactions across multiple computers in a way that is transparent, secure, and immutable. Each transaction, or block, is linked to the previous one through cryptographic hashes, creating a chain of blocks that cannot be altered retroactively. This inherent transparency and immutability make blockchain an ideal solution for maintaining tamper-proof records in industries where data integrity is paramount – such as aviation maintenance.
One of the key advantages of blockchain in aviation maintenance is its ability to provide a single source of truth for maintenance records. Currently, maintenance logs are often fragmented across various stakeholders, including airlines, maintenance providers, regulatory agencies, and equipment manufacturers. This fragmentation can lead to discrepancies, disputes, and delays in maintenance operations. By leveraging blockchain, all maintenance transactions – from routine inspections to component replacements – can be recorded on a shared ledger accessible to authorized parties. This transparent and decentralized approach ensures that all stakeholders have access to the same up-to-date information, minimizing confusion and facilitating collaboration.
Moreover, the tamper-proof nature of blockchain ensures the integrity and authenticity of maintenance records. Each transaction recorded on the blockchain is encrypted and linked to previous transactions, making it virtually impossible to alter or delete without consensus from the network. This level of security eliminates the risk of data tampering, unauthorized access, or manipulation of maintenance records. Additionally, blockchain employs consensus mechanisms such as proof-of-work or proof-of-stake to validate transactions, further enhancing the trustworthiness of the system.
Furthermore, blockchain technology enables real-time access to maintenance records, allowing stakeholders to track the status and history of aircraft and GSE seamlessly. Maintenance logs recorded on the blockchain can include detailed information such as the date, time, location, and personnel involved in each maintenance activity. This granular level of transparency enables airlines to monitor the maintenance history of their fleet in real-time, ensuring compliance with regulatory requirements and industry standards. Similarly, maintenance providers can demonstrate their adherence to service agreements and contractual obligations, fostering trust and accountability in the maintenance process.
Additionally, blockchain technology enables the traceability of components and parts throughout their lifecycle, from manufacturing to retirement. Each component can be assigned a unique digital identity, or "digital twin," recorded on the blockchain along with relevant information such as manufacturer, serial number, maintenance history, and certification status. This digital twin can accompany the physical component throughout its lifespan, providing stakeholders with real-time visibility into its status and provenance. In the event of a safety or quality issue, blockchain enables rapid traceability and recalls, minimizing the impact on operations and ensuring regulatory compliance.
Despite its potential benefits, the widespread adoption of blockchain in aviation maintenance faces several challenges. One of the primary obstacles is the scalability of blockchain networks, particularly in industries with large volumes of transactions and data. The processing power required to validate and record transactions on the blockchain can be substantial, leading to scalability issues and increased operational costs. Additionally, interoperability between different blockchain platforms and legacy systems poses a significant hurdle to integration and adoption.
Furthermore, ensuring data privacy and protection in a blockchain network requires careful consideration of encryption and access control mechanisms. While blockchain offers transparency and immutability, it also raises concerns about the exposure of sensitive information to unauthorized parties. Implementing robust data privacy protocols and compliance frameworks is essential to mitigate these risks and maintain trust in the integrity of the blockchain ecosystem.
In conclusion, blockchain technology holds immense promise for revolutionizing record-keeping in aircraft and ground support equipment (GSE) maintenance. By providing a tamper-proof and transparent ledger system, blockchain streamlines maintenance logs, enhances compliance with regulations, and fosters trust in the integrity of maintenance records. While challenges remain, the potential benefits of blockchain in aviation maintenance are too significant to ignore, making it a compelling solution for the industry's evolving needs. As blockchain continues to mature and gain traction, it is poised to become the gold standard for transparent record-keeping in aviation maintenance, ensuring the safety and reliability of aircraft and GSE for years to come.
4. Augmented Reality (AR) and Virtual Reality (VR) Redefine Maintenance Inspections in Aviation
In the dynamic world of aviation maintenance, precision, efficiency, and safety are paramount. Every inspection, whether it's on an aircraft or ground support equipment (GSE), plays a crucial role in ensuring the reliability and airworthiness of these assets. However, traditional inspection methods often rely on manual processes that can be time-consuming, labor-intensive, and prone to human error. Enter Augmented Reality (AR) and Virtual Reality (VR) technologies – transformative tools that are revolutionizing the inspection process in aviation maintenance. By providing maintenance crews with immersive and interactive experiences, AR and VR are redefining how inspections are conducted, improving accuracy, efficiency, and safety in the maintenance workflow.
At the forefront of this transformation are AR and VR technologies, which offer innovative solutions for visualizing and interacting with complex systems and components. AR overlays digital information onto the physical environment, providing users with real-time contextual information and enhancing their perception of the world around them. VR, on the other hand, immerses users in a computer-generated simulation of a three-dimensional environment, enabling them to interact with virtual objects and spaces. Together, AR and VR technologies offer powerful tools for conducting inspections in both aircraft and GSE maintenance, providing maintenance personnel with enhanced visualization, remote assistance, and training capabilities.
One of the primary advantages of AR and VR in maintenance inspections is their ability to provide maintenance crews with enhanced visualization of complex systems and components. In aircraft maintenance, AR can overlay digital schematics, diagrams, and maintenance procedures onto physical aircraft components, allowing technicians to identify and locate critical systems with greater ease and precision. VR simulations can immerse maintenance personnel in virtual replicas of aircraft interiors and engine compartments, enabling them to conduct detailed inspections without physically accessing the aircraft.
Moreover, AR and VR technologies enable remote assistance capabilities, allowing maintenance personnel to collaborate with experts and colleagues in real-time, regardless of their physical location. AR-powered smart glasses equipped with cameras and displays can transmit live video feeds and AR overlays to remote experts, who can provide guidance, instructions, and annotations to on-site technicians. Similarly, VR-based remote assistance platforms can facilitate virtual collaboration sessions, where multiple users can interact with virtual models and simulations simultaneously, enabling collective problem-solving and knowledge sharing.
Furthermore, AR and VR technologies offer immersive training experiences for maintenance personnel, enabling them to acquire new skills and knowledge in a safe and controlled environment. VR simulations can replicate complex maintenance scenarios, allowing technicians to practice procedures and protocols without risking damage to equipment or personnel. AR-based training modules can provide interactive step-by-step guidance for performing maintenance tasks, enhancing retention and proficiency. Additionally, AR and VR training programs can be tailored to individual learning styles and preferences, maximizing engagement and effectiveness.
One of the key applications of AR and VR in aircraft maintenance inspections is in the field of Non-Destructive Testing (NDT). NDT techniques, such as ultrasonic testing and eddy current inspection, are used to detect defects and anomalies in aircraft structures and components without causing damage. AR and VR technologies can enhance the efficiency and accuracy of NDT inspections by providing technicians with real-time feedback and visualization of inspection results. For example, AR overlays can highlight areas of interest on aircraft surfaces, while VR simulations can visualize internal structures and defects, enabling technicians to make informed decisions about maintenance actions.
Moreover, AR and VR technologies offer significant benefits in GSE maintenance inspections, where equipment such as baggage loaders, aircraft tugs, and ground power units require regular monitoring and upkeep. AR-based maintenance applications can provide technicians with interactive checklists, equipment manuals, and troubleshooting guides, enhancing efficiency and consistency in inspection procedures. VR simulations can replicate the operation of GSE equipment, allowing technicians to practice maintenance tasks and emergency procedures in a realistic virtual environment.
Despite their potential benefits, the widespread adoption of AR and VR in maintenance inspections faces several challenges. One of the primary obstacles is the cost of implementing and integrating AR and VR technologies into existing maintenance workflows. From hardware acquisition to software development and training, the upfront investment required for AR and VR solutions can be significant. Additionally, ensuring compatibility and interoperability with existing maintenance systems and databases requires careful planning and coordination.
Furthermore, the usability and user experience of AR and VR applications can impact their adoption and effectiveness in real-world maintenance scenarios. Designing intuitive interfaces, minimizing latency, and optimizing performance are critical considerations for creating immersive and user-friendly AR and VR experiences. Moreover, addressing concerns about data privacy, security, and regulatory compliance is essential to build trust and confidence in AR and VR technologies, particularly in safety-critical environments such as aviation maintenance.
In conclusion, Augmented Reality (AR) and Virtual Reality (VR) technologies are revolutionizing aircraft and ground support equipment (GSE) maintenance inspections, providing maintenance personnel with enhanced visualization, remote assistance, and training capabilities. By leveraging AR and VR, maintenance organizations can streamline inspection procedures, improve accuracy and efficiency, and enhance the safety and reliability of aviation operations. While challenges remain, the potential benefits of AR and VR in maintenance inspections are too significant to ignore, making them indispensable tools in the modern aviation maintenance toolkit. As AR and VR technologies continue to evolve and mature, their impact on the aviation maintenance industry is poised to grow exponentially, paving the way for a future of safer, more efficient, and more innovative maintenance practices.
5. Embracing Innovation: How 3D Printing Reshapes Spare Parts Management in Aviation Maintenance
In the intricate world of aviation maintenance, efficiency, reliability, and timeliness are paramount. Every aircraft and ground support equipment (GSE) requires meticulous care and upkeep to ensure smooth operations and passenger safety. However, the traditional methods of managing spare parts for these critical assets often come with challenges such as long lead times, high costs, and supply chain disruptions. Enter 3D printing – a transformative technology that is revolutionizing spare parts management in aviation maintenance. By enabling on-site production of components, 3D printing offers a game-changing solution that reduces downtime, lowers costs, and enhances operational readiness like never before.
At its core, 3D printing, also known as additive manufacturing, builds three-dimensional objects layer by layer from digital design files. Unlike traditional manufacturing methods, which rely on subtractive processes such as cutting and molding, 3D printing enables the creation of complex geometries with unparalleled precision and efficiency. This flexibility and agility make 3D printing an ideal solution for producing spare parts on-demand, eliminating the need for extensive warehousing and transportation infrastructure.
One of the primary advantages of 3D printing in spare parts management is its ability to overcome supply chain constraints and logistical challenges. In the aviation industry, spare parts are often sourced from a network of suppliers located around the world, leading to lengthy procurement lead times and shipping delays. However, with 3D printing, spare parts can be produced locally, on-site, or on-demand, eliminating the need for extensive warehousing and transportation infrastructure. This decentralized production model enables maintenance organizations to respond rapidly to changing demands and unforeseen contingencies, minimizing downtime and maximizing asset uptime.
Moreover, 3D printing offers significant cost savings compared to traditional manufacturing methods, particularly for low-volume and high-complexity parts. Traditional manufacturing processes, such as injection molding and machining, require expensive tooling and setup costs, making them economically unfeasible for producing small batches of spare parts. In contrast, 3D printing requires minimal setup and tooling, allowing for cost-effective production of custom and on-demand parts with minimal waste. Additionally, the ability to consolidate multiple components into a single printed part further reduces material costs and assembly time, resulting in overall cost savings for maintenance operations.
Furthermore, 3D printing enables rapid prototyping and iteration of spare parts, accelerating the design and development process. Traditional manufacturing methods often involve lengthy lead times for tooling and production setup, making it difficult to iterate and refine designs quickly. However, with 3D printing, designers can produce functional prototypes in a matter of hours, allowing for rapid validation of design concepts and optimization of part performance. This iterative approach not only speeds up the development cycle but also ensures that spare parts meet the specific requirements and specifications of the application, resulting in higher quality and reliability.
Another significant advantage of 3D printing in spare parts management is its potential to unlock new design possibilities and performance enhancements. Traditional manufacturing methods impose limitations on the design of spare parts due to constraints such as tooling requirements and material properties. However, 3D printing enables designers to create complex geometries and lattice structures that are impossible to achieve with traditional methods, allowing for lightweighting, optimization of material usage, and improved functional performance. Additionally, the ability to use a wide range of materials, including advanced composites and polymers, opens up new opportunities for enhancing the durability, reliability, and longevity of spare parts in harsh operating environments.
In the realm of aircraft maintenance, 3D printing offers unique benefits for managing obsolete and hard-to-find parts. As aircraft age, certain components may become obsolete or no longer supported by manufacturers, making it challenging to source replacement parts through traditional channels. However, with 3D printing, maintenance organizations can recreate these parts from digital designs, ensuring that critical assets remain operational and airworthy. This capability not only extends the lifespan of aging aircraft but also reduces reliance on costly and time-consuming supply chain alternatives, such as reverse engineering or aftermarket suppliers.
Similarly, in ground support equipment (GSE) maintenance, 3D printing provides a game-changing solution for addressing equipment downtime and obsolescence issues. GSE encompasses a wide range of equipment, including baggage loaders, aircraft tugs, and ground power units, each with its own unique set of spare part requirements. By leveraging 3D printing, maintenance organizations can produce custom and on-demand parts for GSE quickly and cost-effectively, ensuring that equipment remains operational and operational readiness is maintained at all times.
Despite its numerous advantages, the widespread adoption of 3D printing in spare parts management faces several challenges. One of the primary obstacles is the need for robust quality assurance and certification processes to ensure that printed parts meet regulatory and safety standards. Additionally, optimizing printing parameters and material properties to achieve desired performance characteristics can be complex and time-consuming, requiring expertise and experimentation. Moreover, intellectual property concerns, such as copyright infringement and unauthorized replication of proprietary designs, must be addressed to protect the interests of original equipment manufacturers and designers.
Furthermore, the scalability and throughput of 3D printing technologies are still evolving, particularly for large-scale production of high-volume parts. While 3D printing excels in producing low-volume and customized parts, achieving economies of scale for mass production remains a challenge. Additionally, the availability of qualified materials and certified printing processes for aerospace applications is limited, constraining the range of parts that can be produced using 3D printing.
In conclusion, 3D printing is revolutionizing spare parts management in aircraft and ground support equipment (GSE) maintenance, offering a faster, more cost-effective, and sustainable alternative to traditional manufacturing methods. By enabling on-demand production of custom and obsolete parts, 3D printing enhances operational readiness, reduces downtime, and improves asset uptime for aviation maintenance organizations. While challenges remain, the potential benefits of 3D printing in spare parts management are too significant to ignore, making it a transformative technology in the pursuit of efficiency, reliability, and innovation in the aviation industry. As 3D printing continues to evolve and mature, its role in spare parts management is poised to expand, unlocking new opportunities and driving further advancements in aviation maintenance practices.
6. Harnessing Drone Technology for Aircraft and GSE Maintenance Inspections
In the ever-evolving landscape of aviation maintenance, innovation is the key to staying ahead. As aircraft and ground support equipment (GSE) become increasingly complex, traditional inspection methods are being challenged to keep pace. Enter drone technology – a game-changing solution that is revolutionizing the way maintenance inspections are conducted. From aerial surveys to close-up inspections, drones offer a versatile and efficient approach to monitoring and maintaining critical assets in the aviation industry.
Drones, also known as Unmanned Aerial Vehicles (UAVs), are remotely piloted aircraft equipped with cameras, sensors, and other advanced technology. These compact and agile devices can access areas that are difficult or dangerous for humans to reach, making them ideal for conducting inspections of aircraft and GSE. Whether it's inspecting aircraft exteriors for damage or assessing the condition of runway lighting systems, drones provide maintenance personnel with a bird's-eye view of critical assets, enabling them to identify issues quickly and accurately.
One of the primary advantages of using drones for maintenance inspections is their ability to access hard-to-reach areas with ease. Aircraft exteriors, for example, can be challenging to inspect thoroughly due to their height and complex geometries. Traditional inspection methods often involve manual visual inspections conducted from scaffolding or cherry pickers, which can be time-consuming and labor-intensive. In contrast, drones can fly close to the aircraft, capturing high-resolution images and videos of critical areas such as wings, fuselage, and engine nacelles, without the need for costly equipment or putting personnel at risk.
Moreover, drones offer significant time and cost savings compared to traditional inspection methods. Manual inspections require extensive preparation, including erecting scaffolding, setting up safety equipment, and coordinating personnel. In contrast, drones can be deployed quickly and easily, reducing inspection lead times and minimizing disruption to operations. Additionally, drones can cover large areas in a fraction of the time it would take for humans to conduct inspections manually, enabling maintenance teams to inspect multiple aircraft or GSE in a single deployment.
Furthermore, drones provide maintenance personnel with real-time situational awareness and actionable insights during inspections. Equipped with high-resolution cameras, thermal imaging sensors, and other specialized equipment, drones can detect and capture subtle signs of damage or wear that may go unnoticed by the naked eye. Advanced imaging algorithms and machine learning techniques can analyze drone data in real-time, flagging potential issues and anomalies for further investigation. This proactive approach to inspections enables maintenance teams to identify problems early, prioritize repairs, and prevent costly downtime.
Another key advantage of using drones for maintenance inspections is their ability to enhance safety and reduce risk for maintenance personnel. Manual inspections often involve working at height or in hazardous environments, exposing personnel to risks such as falls, electrocution, and exposure to harsh weather conditions. Drones eliminate the need for personnel to access dangerous areas directly, minimizing the risk of accidents and injuries. Additionally, drones can be equipped with collision avoidance systems and GPS tracking capabilities, further enhancing safety and control during flight operations.
In the realm of aircraft maintenance, drones offer unique capabilities for inspecting critical components such as engines, wings, and landing gear. Thermal imaging sensors, for example, can detect hotspots and abnormalities in engine components, indicating potential issues such as overheating or oil leaks. LiDAR (Light Detection and Ranging) technology can create detailed 3D maps of aircraft structures, enabling engineers to identify deformities or structural damage. Moreover, drones equipped with gas detection sensors can monitor for leaks in fuel systems and hydraulic lines, ensuring the safety and airworthiness of the aircraft.
Similarly, in GSE maintenance, drones provide valuable insights into the condition of equipment such as baggage loaders, aircraft tugs, and ground power units. Visual inspections conducted by drones can identify wear and tear on moving parts, corrosion on metal surfaces, and damage to electrical components. Thermal imaging sensors can detect overheating in motors and electrical systems, indicating potential faults or impending failures. Additionally, drones equipped with LiDAR technology can create digital models of equipment, enabling engineers to assess structural integrity and plan maintenance activities more effectively.
Despite their numerous advantages, the widespread adoption of drones for maintenance inspections faces several challenges. One of the primary obstacles is regulatory compliance and airspace management. Aviation authorities such as the Federal Aviation Administration (FAA) and the European Union Aviation Safety Agency (EASA) have stringent regulations governing the operation of drones in commercial airspace, particularly around airports and other sensitive areas. Ensuring compliance with these regulations requires careful planning and coordination between maintenance organizations, drone operators, and regulatory authorities.
Moreover, the scalability and integration of drone technology into existing maintenance workflows pose challenges for adoption. Implementing drones as a standard tool for inspections requires investment in training, equipment, and infrastructure, as well as changes to operational procedures and protocols. Additionally, ensuring data security and privacy during drone operations is essential to protect sensitive information and prevent unauthorized access or tampering.
Furthermore, the reliability and performance of drone technology in adverse weather conditions and harsh environments can impact its effectiveness for maintenance inspections. High winds, rain, and extreme temperatures can affect drone stability and sensor accuracy, limiting their utility in certain situations. Additionally, battery life and flight endurance may be insufficient for conducting prolonged or extensive inspections, requiring careful planning and optimization of flight operations.
In conclusion, drones are revolutionizing aircraft and ground support equipment (GSE) maintenance inspections, offering a versatile, efficient, and cost-effective solution for monitoring critical assets in the aviation industry. By providing maintenance personnel with access to hard-to-reach areas, real-time situational awareness, and enhanced safety, drones enable proactive maintenance practices that minimize downtime and maximize operational readiness. While challenges remain, the potential benefits of drones for maintenance inspections are too significant to ignore, making them an indispensable tool in the modern aviation maintenance toolkit. As drone technology continues to evolve and mature, its role in maintenance inspections is poised to expand, unlocking new opportunities and driving further advancements in aviation maintenance practices.
7. The Advent of Autonomous Maintenance Vehicles on the Tarmac
In the bustling environment of airports, where every minute counts and precision is paramount, the need for innovative solutions to streamline maintenance operations has never been more pressing. Enter Autonomous Maintenance Vehicles (AMVs) – the future of tarmac maintenance. Imagine a fleet of autonomous vehicles seamlessly navigating the tarmac, conducting routine maintenance tasks on both aircraft and ground support equipment (GSE). Equipped with cutting-edge technology, these vehicles are set to revolutionize maintenance operations, enhancing efficiency, and reducing turnaround times like never before.
At the heart of this transformation are AMVs – self-driving vehicles designed to perform a range of maintenance tasks autonomously. Leveraging a combination of sensors, cameras, LiDAR, and advanced algorithms, AMVs can navigate complex environments, avoid obstacles, and execute predefined tasks with precision. From refueling aircraft to inspecting GSE, these vehicles offer a versatile and efficient solution for tarmac maintenance.
One of the primary advantages of using AMVs is their ability to operate autonomously around the clock, without the need for human intervention. Traditional maintenance operations often rely on manual labor, which is subject to limitations such as fatigue, human error, and availability. In contrast, AMVs can work tirelessly 24/7, maximizing productivity and minimizing downtime. This continuous operation ensures that maintenance tasks are completed in a timely manner, contributing to faster turnaround times for aircraft and GSE.
Moreover, AMVs offer significant safety benefits compared to traditional maintenance methods. Human workers performing maintenance tasks on the tarmac are exposed to various hazards, including moving aircraft, heavy equipment, and inclement weather conditions. By replacing manual labor with autonomous vehicles, the risk of accidents and injuries is greatly reduced. AMVs are equipped with advanced safety features such as collision avoidance systems and emergency braking capabilities, ensuring safe operation in dynamic environments.
Furthermore, AMVs are highly adaptable and can be customized to perform a wide range of maintenance tasks. From refueling and de-icing aircraft to inspecting tires and brakes on GSE, AMVs can handle diverse responsibilities with ease. These vehicles can be equipped with specialized tools and equipment tailored to specific maintenance requirements, maximizing efficiency and versatility. Additionally, AMVs can be programmed to follow predefined routes and schedules, optimizing workflow and resource allocation.
Another key advantage of using AMVs for tarmac maintenance is their ability to collect and analyze data in real-time. Equipped with sensors and cameras, AMVs can capture valuable information about the condition and performance of aircraft and GSE during maintenance operations. This data can be transmitted to maintenance crews and decision-makers in real-time, enabling proactive decision-making and optimization of maintenance processes. By harnessing the power of data analytics and machine learning, AMVs can identify patterns, trends, and anomalies, leading to more efficient and effective maintenance strategies.
In the realm of aircraft maintenance, AMVs offer unique capabilities for conducting routine inspections and servicing tasks. These vehicles can autonomously navigate the tarmac, conducting visual inspections of aircraft exteriors for signs of damage or wear. They can also perform tasks such as checking fluid levels, inspecting engine components, and servicing onboard systems, all without the need for human intervention. By automating these routine maintenance tasks, AMVs free up human resources to focus on more complex and specialized maintenance activities.
Similarly, in GSE maintenance, AMVs provide valuable support for inspecting, servicing, and repairing equipment such as baggage loaders, aircraft tugs, and ground power units. These vehicles can autonomously patrol the tarmac, conducting visual inspections of GSE for signs of wear, damage, or malfunction. They can also perform routine maintenance tasks such as lubricating moving parts, replacing worn-out components, and conducting diagnostic tests, all while minimizing disruption to operations.
Despite their numerous advantages, the widespread adoption of AMVs in tarmac maintenance faces several challenges. One of the primary obstacles is regulatory compliance and certification. Autonomous vehicles operating on the tarmac must adhere to strict safety standards and regulations imposed by aviation authorities such as the Federal Aviation Administration (FAA) and the European Union Aviation Safety Agency (EASA). Ensuring compliance with these regulations requires rigorous testing, validation, and certification of AMVs and their systems.
Moreover, integrating AMVs into existing maintenance workflows and infrastructure requires careful planning and coordination. Maintenance operations on the tarmac are complex and dynamic, involving multiple stakeholders, equipment, and procedures. Deploying AMVs alongside human workers and traditional maintenance vehicles requires seamless integration and synchronization to ensure safety and efficiency. Additionally, ensuring interoperability and compatibility with existing systems and equipment is essential for maximizing the effectiveness of AMVs in tarmac maintenance operations.
Furthermore, addressing concerns about cybersecurity and data privacy is essential to protect sensitive information transmitted and stored by AMVs. These vehicles rely on wireless communication networks and cloud-based systems to transmit data and receive instructions. Securing these communication channels and implementing robust encryption and authentication mechanisms are crucial to prevent unauthorized access or tampering of data.
In conclusion, Autonomous Maintenance Vehicles (AMVs) are poised to revolutionize tarmac maintenance operations, offering a versatile, efficient, and safe solution for conducting routine maintenance tasks on both aircraft and ground support equipment (GSE). By leveraging advanced technology and automation, AMVs enhance efficiency, reduce turnaround times, and improve safety in maintenance operations. While challenges remain, the potential benefits of AMVs for tarmac maintenance operations are too significant to ignore, making them an indispensable tool in the modern aviation maintenance toolkit. As AMV technology continues to evolve and mature, its role in tarmac maintenance operations is poised to expand, unlocking new opportunities for efficiency, reliability, and safety on the tarmac.
8. How Cloud-Based Maintenance Systems Revolutionize Collaboration in Aviation Maintenance
In the fast-paced world of aviation maintenance, precision, efficiency, and collaboration are essential to ensuring the safety and reliability of aircraft and ground support equipment (GSE). As technology continues to evolve, so too does the way maintenance data is managed and shared among stakeholders. Enter cloud-based maintenance systems – transformative solutions that are revolutionizing collaboration in the aviation maintenance industry. By leveraging the power of the cloud, these systems are streamlining data storage, enabling real-time access, and fostering collaboration among maintenance teams, regardless of their geographical location.
At the core of this transformation are cloud-based maintenance systems, which provide a centralized platform for storing, managing, and sharing maintenance data. Unlike traditional on-premise systems, which are limited by physical hardware and storage capacity, cloud-based systems offer virtually unlimited scalability and accessibility. Maintenance data, including work orders, inspection reports, maintenance schedules, and equipment histories, can be securely stored and accessed from anywhere with an internet connection, empowering maintenance teams to work more efficiently and collaboratively.
One of the primary advantages of cloud-based maintenance systems is their ability to centralize and standardize maintenance data across an organization. In the past, maintenance data was often fragmented across disparate systems and databases, making it difficult to access and share information across departments and locations. With cloud-based systems, all maintenance data is stored in a single, centralized repository, providing a unified source of truth for maintenance operations. This centralized approach ensures consistency, accuracy, and completeness of maintenance records, enabling stakeholders to make informed decisions based on reliable data.
Moreover, cloud-based maintenance systems offer real-time access to maintenance data, enabling stakeholders to collaborate more effectively and respond rapidly to changing conditions. Maintenance teams can access up-to-date information on aircraft and GSE status, maintenance tasks, and inspection results from anywhere at any time, using a variety of devices such as laptops, tablets, and smartphones. This accessibility fosters real-time collaboration among maintenance personnel, enabling them to coordinate tasks, share insights, and troubleshoot issues more efficiently.
Furthermore, cloud-based maintenance systems facilitate seamless collaboration among stakeholders, including airlines, maintenance providers, OEMs (Original Equipment Manufacturers), regulatory agencies, and other third-party partners. By providing a centralized platform for sharing maintenance data, these systems break down silos and barriers to collaboration, enabling stakeholders to work together more effectively towards common goals such as improving safety, reliability, and operational efficiency. For example, airlines can share maintenance data with their maintenance providers in real-time, enabling proactive maintenance planning and execution. Similarly, OEMs can access maintenance data to monitor equipment performance and provide timely support and guidance to their customers.
Another significant benefit of cloud-based maintenance systems is their ability to facilitate remote monitoring and diagnostics of aircraft and GSE. By leveraging sensors and IoT (Internet of Things) devices installed on aircraft and GSE, maintenance data such as engine performance, fuel consumption, and component health can be collected and transmitted to the cloud in real-time. Maintenance personnel can then analyze this data remotely, identify potential issues, and take proactive measures to address them before they escalate. This proactive approach to maintenance reduces the risk of unscheduled downtime and enhances the reliability of aircraft and GSE.
In the realm of aircraft maintenance, cloud-based systems offer unique capabilities for managing maintenance tasks, schedules, and resources. Maintenance crews can access their work orders, task lists, and documentation from the cloud, eliminating the need for paper-based or manual processes. Real-time updates and notifications ensure that maintenance teams are always aware of their assignments and priorities, enabling them to work more efficiently and effectively. Additionally, cloud-based systems can automate routine maintenance tasks, such as scheduling inspections and generating work orders, freeing up maintenance personnel to focus on more complex and critical tasks.
Similarly, in GSE maintenance, cloud-based systems provide valuable support for managing equipment fleets, tracking maintenance activities, and optimizing resource utilization. Maintenance managers can monitor the performance and health of GSE in real-time, identify maintenance trends and patterns, and make data-driven decisions to improve reliability and efficiency. Additionally, cloud-based systems can streamline inventory management and procurement processes, ensuring that spare parts and supplies are readily available when needed, minimizing equipment downtime and disruptions to operations.
Despite their numerous advantages, the widespread adoption of cloud-based maintenance systems faces several challenges. One of the primary obstacles is data security and privacy concerns, particularly in industries such as aviation where sensitive information is involved. Ensuring the confidentiality, integrity, and availability of maintenance data stored in the cloud requires robust encryption, access controls, and compliance with industry regulations such as GDPR (General Data Protection Regulation) and HIPAA (Health Insurance Portability and Accountability Act).
Moreover, addressing concerns about data ownership, sovereignty, and vendor lock-in is essential to build trust and confidence in cloud-based maintenance systems. Maintenance organizations must carefully evaluate cloud service providers and negotiate service level agreements (SLAs) to ensure that their data remains under their control and is protected against unauthorized access or disclosure. Additionally, maintaining data interoperability and compatibility with legacy systems and industry standards is crucial to ensure seamless integration and migration to cloud-based solutions.
In conclusion, cloud-based maintenance systems are transforming collaboration in the aviation maintenance industry, enabling stakeholders to store, manage, and share maintenance data more efficiently and effectively. By providing a centralized platform for real-time access to maintenance data, these systems break down silos and barriers to collaboration, enabling stakeholders to work together towards common goals. While challenges remain, the potential benefits of cloud-based maintenance systems are too significant to ignore, making them an essential tool for improving safety, reliability, and efficiency in aviation maintenance operations. As technology continues to evolve and mature, the role of cloud-based maintenance systems in the aviation industry is poised to expand, unlocking new opportunities for innovation and collaboration in the pursuit of excellence in maintenance practices.
9. The Imperative of Cybersecurity Prioritization for Aircraft and GSE Maintenance
In today's increasingly interconnected world, where digital systems and technologies play a central role in aviation operations, the importance of cybersecurity in aircraft and ground support equipment (GSE) maintenance cannot be overstated. As aircraft and GSE become more reliant on digital systems for critical functions, they also become more vulnerable to cyber threats that could compromise safety, reliability, and operational integrity. Thus, robust cybersecurity measures are no longer optional but imperative to safeguard against potential cyberattacks and ensure the continued safety and security of aviation operations.
The integration of digital systems and technologies into modern aircraft and GSE has brought about numerous benefits, including improved efficiency, enhanced functionality, and advanced capabilities. From flight management systems to engine control units, these digital systems play a crucial role in monitoring, controlling, and managing various aspects of aircraft and GSE operations. However, with these benefits also come inherent risks, as digital systems are susceptible to cyber threats such as hacking, malware, and unauthorized access.
One of the primary reasons for the growing importance of cybersecurity in aircraft and GSE maintenance is the increasing connectivity of these systems to external networks and the internet. With the advent of the Internet of Things (IoT) and the proliferation of connected devices, aircraft and GSE are now more interconnected than ever before. While this connectivity offers numerous benefits, including remote monitoring, predictive maintenance, and data analytics, it also introduces new vulnerabilities that could be exploited by malicious actors.
Moreover, the reliance on third-party vendors and suppliers for digital systems and components further complicates cybersecurity in aircraft and GSE maintenance. As aircraft and GSE incorporate a multitude of digital systems and components sourced from various vendors, ensuring the security of each component and subsystem becomes a significant challenge. Vulnerabilities in one component or subsystem could potentially compromise the entire aircraft or GSE system, highlighting the importance of a holistic and integrated approach to cybersecurity.
In response to these challenges, aviation maintenance organizations must prioritize cybersecurity as an integral part of their maintenance practices and procedures. This includes implementing robust security measures to protect aircraft and GSE against cyber threats, as well as developing comprehensive cybersecurity policies and protocols to mitigate risks and vulnerabilities. Key cybersecurity measures for aircraft and GSE maintenance include:
1. Access Control: Implementing strict access controls to limit access to critical systems and components only to authorized personnel. This includes the use of strong authentication mechanisms such as multi-factor authentication and biometric verification to prevent unauthorized access.
2. Encryption: Encrypting sensitive data both in transit and at rest to protect it from unauthorized access or interception. This includes encrypting communications between aircraft and ground systems, as well as encrypting data stored on onboard computers and servers.
3.Intrusion Detection and Prevention Systems (IDPS): Deploying IDPS to monitor network traffic and detect potential cyber threats in real-time. IDPS can identify and block suspicious activities, such as unauthorized access attempts or malware infections, before they can cause harm to aircraft or GSE systems.
4. Regular Software Updates and Patch Management: Ensuring that all software and firmware installed on aircraft and GSE are up-to-date with the latest security patches and updates. This helps to mitigate known vulnerabilities and reduce the risk of exploitation by cyber attackers.
5.Security Awareness Training: Providing comprehensive training and awareness programs to maintenance personnel on cybersecurity best practices and procedures. This includes educating personnel on how to recognize and report potential security threats, as well as promoting a culture of cybersecurity awareness and vigilance.
6. Incident Response Planning: Developing detailed incident response plans and procedures to address cyber incidents in a timely and effective manner. This includes establishing clear roles and responsibilities, defining escalation procedures, and conducting regular drills and exercises to test the organization's response capabilities.
Furthermore, collaboration and information sharing among aviation stakeholders are essential for effectively addressing cybersecurity threats in aircraft and GSE maintenance. This includes sharing threat intelligence, best practices, and lessons learned with other maintenance organizations, regulatory agencies, and industry partners. By working together, the aviation industry can develop a collective defense posture against cyber threats and enhance the overall security and resilience of aviation operations.
In conclusion, cybersecurity is a non-negotiable aspect of aircraft and GSE maintenance in today's digital age. As aircraft and GSE become more reliant on digital systems for critical functions, they also become more vulnerable to cyber threats that could compromise safety, reliability, and operational integrity. Therefore, aviation maintenance organizations must prioritize cybersecurity as an integral part of their maintenance practices and procedures. By implementing robust security measures, developing comprehensive cybersecurity policies and protocols, and fostering collaboration and information sharing among aviation stakeholders, the industry can effectively mitigate cyber risks and ensure the continued safety and security of aviation operations.
10. The Power of Integrated Ecosystems for Holistic Maintenance
In the ever-evolving landscape of aviation maintenance, the quest for efficiency, reliability, and safety is a never-ending journey. As technology continues to advance, the integration of disparate systems and processes into cohesive ecosystems has emerged as a game-changer in optimizing maintenance operations. One such innovation is the concept of integrated ecosystems for holistic maintenance, where aircraft and ground support equipment (GSE) maintenance software seamlessly integrates with other aviation systems to create a unified and interconnected platform. This integration not only streamlines processes but also enhances collaboration, data accuracy, and decision-making across the entire aviation ecosystem.
At the heart of this transformation are integrated maintenance software solutions that serve as the backbone of the holistic maintenance ecosystem. These software platforms are designed to centralize and consolidate maintenance data, processes, and workflows, providing a single source of truth for all stakeholders involved in aircraft and GSE maintenance. By integrating with other aviation systems such as flight planning, crew scheduling, and inventory management, these platforms enable end-to-end visibility and control over maintenance operations, from planning and scheduling to execution and analysis.
One of the primary benefits of integrated maintenance ecosystems is their ability to optimize maintenance processes and workflows. By seamlessly integrating maintenance software with other aviation systems, maintenance tasks can be automatically triggered based on flight schedules, crew availability, and equipment status. For example, when a flight is scheduled, the maintenance system can automatically generate maintenance tasks for the aircraft and allocate resources based on predefined rules and priorities. This automation not only reduces manual intervention but also minimizes downtime and maximizes asset utilization, leading to cost savings and operational efficiency.
Moreover, integrated maintenance ecosystems facilitate real-time collaboration and communication among stakeholders, both within and across organizational boundaries. Maintenance data, such as work orders, task assignments, and equipment status, can be shared and accessed in real-time by maintenance crews, flight operations, and ground personnel, regardless of their geographical location. This real-time visibility enables proactive decision-making, rapid response to operational disruptions, and seamless coordination of maintenance activities, ultimately improving overall operational efficiency and reliability.
Furthermore, integrated maintenance ecosystems enhance data accuracy and integrity by eliminating duplicate data entry and ensuring data consistency across different systems and applications. Maintenance data is entered once and automatically synchronized across all integrated systems, reducing the risk of errors, discrepancies, and inconsistencies. This single source of truth ensures that all stakeholders have access to the most up-to-date and accurate information, enabling them to make informed decisions with confidence.
Additionally, integrated maintenance ecosystems enable data-driven decision-making by providing access to actionable insights and analytics derived from maintenance data. By leveraging advanced analytics and machine learning algorithms, maintenance organizations can identify patterns, trends, and anomalies in maintenance data, enabling them to optimize maintenance schedules, predict equipment failures, and prioritize maintenance tasks based on risk and impact. These predictive and prescriptive analytics empower maintenance organizations to proactively manage maintenance operations and minimize unplanned downtime, ultimately improving aircraft and GSE reliability and availability.
In the realm of aircraft maintenance, integrated ecosystems offer unique capabilities for managing complex maintenance tasks and activities. Maintenance crews can access comprehensive dashboards and interactive displays that provide real-time visibility into aircraft status, maintenance schedules, and performance metrics. From conducting routine inspections to performing major overhauls, maintenance tasks can be planned, scheduled, and executed with precision and efficiency, ensuring that aircraft remain safe, airworthy, and operational at all times.
Similarly, in GSE maintenance, integrated ecosystems provide valuable support for managing equipment fleets, tracking maintenance activities, and optimizing resource utilization. Maintenance managers can monitor the performance and health of GSE in real-time, identify maintenance trends and patterns, and make data-driven decisions to improve reliability and efficiency. Additionally, integrated ecosystems can streamline inventory management and procurement processes, ensuring that spare parts and supplies are readily available when needed, minimizing equipment downtime and disruptions to operations.
Despite their numerous advantages, the implementation of integrated maintenance ecosystems faces several challenges. One of the primary obstacles is the complexity of integrating disparate systems and applications with varying data formats, protocols, and standards. Ensuring seamless interoperability and compatibility between different systems requires careful planning, coordination, and integration expertise. Moreover, addressing concerns about data security, privacy, and regulatory compliance is essential to protect sensitive information and ensure compliance with industry regulations and standards.
In conclusion, integrated ecosystems for holistic maintenance are revolutionizing aircraft and ground support equipment maintenance operations, enabling seamless integration of maintenance software with other aviation systems to create a unified and interconnected platform. By optimizing processes, enhancing collaboration, and enabling data-driven decision-making, these ecosystems improve operational efficiency, reliability, and safety across the entire aviation ecosystem. While challenges remain, the potential benefits of integrated maintenance ecosystems are too significant to ignore, making them an indispensable tool for modernizing and optimizing aviation maintenance operations. As technology continues to evolve and mature, the role of integrated ecosystems in aviation maintenance is poised to expand, unlocking new opportunities for innovation and excellence in maintenance practices.
11. How Machine Learning Optimizes Resource Allocation in Aircraft and GSE Maintenance
In the dynamic and complex world of aviation maintenance, efficiency, reliability, and cost-effectiveness are paramount. As aircraft fleets and ground support equipment (GSE) continue to grow and evolve, the challenge of optimizing maintenance schedules and resource allocation becomes increasingly critical. Traditional methods of maintenance planning often rely on fixed schedules or reactive approaches, leading to inefficiencies and unnecessary costs. However, with the advent of machine learning, a new era of intelligent maintenance optimization is emerging. By leveraging historical data and predictive analytics, machine learning algorithms can forecast optimal maintenance schedules for both aircraft and GSE, leading to more efficient resource allocation and reduced operational costs.
At the heart of this transformation are machine learning algorithms, a subset of artificial intelligence (AI) that enables computers to learn from historical data, identify patterns, and make predictions or decisions with minimal human intervention. By analyzing vast amounts of historical maintenance data, including equipment performance, maintenance records, and operational parameters, machine learning algorithms can uncover hidden insights and trends that traditional methods may overlook. This predictive capability allows maintenance organizations to anticipate maintenance needs, optimize resource allocation, and minimize downtime, ultimately improving operational efficiency and reducing costs.
One of the primary benefits of machine learning in aircraft and GSE maintenance is its ability to predict optimal maintenance schedules based on historical data and equipment performance. By analyzing patterns and trends in maintenance data, machine learning algorithms can identify the optimal timing for maintenance tasks such as inspections, repairs, and component replacements. This proactive approach to maintenance planning minimizes the risk of unexpected failures and breakdowns, leading to more reliable and efficient operations.
Moreover, machine learning enables maintenance organizations to optimize resource allocation by matching maintenance tasks with available resources such as manpower, equipment, and materials. By considering factors such as skill levels, availability, and workload capacity, machine learning algorithms can identify the most efficient allocation of resources to maximize productivity and minimize costs. For example, maintenance crews can be deployed strategically based on predicted maintenance needs and priority levels, ensuring that critical tasks are addressed promptly while avoiding unnecessary downtime or overutilization of resources.
Furthermore, machine learning algorithms can adapt and improve over time as they are exposed to new data and feedback. By continuously learning from real-world maintenance scenarios and outcomes, these algorithms can refine their predictions and recommendations, leading to increasingly accurate and reliable results. This iterative learning process allows maintenance organizations to continuously optimize their maintenance schedules and resource allocation strategies, staying ahead of evolving operational challenges and requirements.
In the realm of aircraft maintenance, machine learning offers unique capabilities for optimizing maintenance schedules and resource allocation for diverse fleets of aircraft. By analyzing historical maintenance data and flight schedules, machine learning algorithms can predict optimal maintenance intervals based on factors such as aircraft usage, operating conditions, and component wear. These predictions enable maintenance organizations to schedule maintenance tasks more efficiently, reducing aircraft downtime and maximizing fleet availability.
Similarly, in GSE maintenance, machine learning provides valuable support for optimizing resource allocation and minimizing downtime. By analyzing historical maintenance data and equipment usage patterns, machine learning algorithms can forecast optimal maintenance schedules for GSE such as baggage loaders, aircraft tugs, and ground power units. These predictions enable maintenance organizations to allocate resources more effectively, ensuring that GSE remains operational and available when needed.
Despite their numerous advantages, the successful implementation of machine learning in aircraft and GSE maintenance requires careful planning, data management, and integration with existing systems and processes. Maintenance organizations must ensure that they have access to high-quality, reliable data for training machine learning algorithms and validating their predictions. Additionally, addressing concerns about data privacy, security, and regulatory compliance is essential to protect sensitive information and ensure compliance with industry regulations and standards.
In conclusion, machine learning is revolutionizing aircraft and GSE maintenance by optimizing resource allocation and improving operational efficiency. By leveraging historical data and predictive analytics, machine learning algorithms can forecast optimal maintenance schedules, enabling maintenance organizations to allocate resources more effectively, minimize downtime, and reduce operational costs. While challenges remain, the potential benefits of machine learning in aircraft and GSE maintenance are too significant to ignore, making it an indispensable tool for modernizing and optimizing maintenance operations. As technology continues to evolve and mature, the role of machine learning in aviation maintenance is poised to expand, unlocking new opportunities for innovation and excellence in maintenance practices.
12. IoT Sensors for Real-Time Monitoring in Aircraft and GSE Maintenance
In the fast-paced world of aviation maintenance, the ability to monitor and manage the health and performance of aircraft and ground support equipment (GSE) in real-time is crucial for ensuring safety, reliability, and efficiency. With the advent of Internet of Things (IoT) technology, a new era of connectivity and intelligence is revolutionizing maintenance operations. By embedding IoT sensors in various components of aircraft and GSE, maintenance personnel can access a constant stream of real-time data, enabling precise monitoring and proactive maintenance interventions. In this blog post, we'll explore how IoT sensors are transforming aircraft and GSE maintenance through real-time monitoring and data-driven decision-making.
At the heart of the IoT revolution in maintenance are sensors – small, wireless devices capable of collecting and transmitting data from various components and systems. These sensors can be embedded in critical aircraft components such as engines, avionics systems, and structural elements, as well as in GSE components such as engines, hydraulics, and electronics. By continuously monitoring parameters such as temperature, pressure, vibration, and performance metrics, IoT sensors provide maintenance personnel with valuable insights into the health and condition of aircraft and GSE systems in real-time.
One of the primary benefits of IoT sensors in aircraft and GSE maintenance is their ability to enable proactive maintenance interventions by detecting anomalies and potential issues before they escalate. By continuously monitoring key parameters and performance metrics, IoT sensors can identify deviations from normal operating conditions, indicating potential faults or malfunctions. Maintenance personnel can then be alerted in real-time to investigate the issue further and take corrective action, preventing unexpected failures and minimizing downtime.
Moreover, IoT sensors provide maintenance personnel with unprecedented visibility into the operational status and performance of aircraft and GSE systems. By capturing data in real-time and transmitting it to centralized monitoring systems, IoT sensors enable maintenance personnel to monitor critical systems and components remotely, from anywhere with an internet connection. This remote monitoring capability allows maintenance teams to stay informed about the health and condition of aircraft and GSE systems, even when they are in operation or located in remote locations.
Furthermore, IoT sensors facilitate condition-based maintenance strategies by providing maintenance personnel with actionable insights derived from real-time data. By analyzing trends and patterns in sensor data, maintenance personnel can identify potential maintenance needs and prioritize tasks based on the condition and performance of critical components. This data-driven approach to maintenance planning enables maintenance organizations to optimize their resources, minimize downtime, and extend the lifespan of aircraft and GSE systems.
In the realm of aircraft maintenance, IoT sensors offer unique capabilities for monitoring the health and performance of critical systems and components. For example, sensors embedded in aircraft engines can continuously monitor parameters such as temperature, pressure, and vibration, providing early warning of potential engine faults or failures.
Similarly, sensors installed in avionics systems can monitor system performance and detect anomalies that could indicate potential issues with navigation, communication, or flight control systems. Similarly, in GSE maintenance, IoT sensors provide valuable insights into the condition and performance of equipment such as baggage loaders, aircraft tugs, and ground power units. By monitoring parameters such as engine temperature, hydraulic pressure, and battery voltage, sensors can detect anomalies and potential faults in GSE components, enabling maintenance personnel to take proactive measures to address them before they escalate.
Despite their numerous advantages, the widespread adoption of IoT sensors in aircraft and GSE maintenance faces several challenges. One of the primary obstacles is the complexity of integrating IoT sensors with existing aircraft and GSE systems and infrastructure. Ensuring seamless interoperability and compatibility between sensors and onboard systems requires careful planning, coordination, and integration expertise. Additionally, addressing concerns about data security, privacy, and regulatory compliance is essential to protect sensitive information and ensure compliance with industry regulations and standards.
In conclusion, IoT sensors are revolutionizing aircraft and GSE maintenance by enabling real-time monitoring and data-driven decision-making. By continuously monitoring key parameters and performance metrics, IoT sensors provide maintenance personnel with valuable insights into the health and condition of aircraft and GSE systems, enabling proactive maintenance interventions and minimizing downtime. While challenges remain, the potential benefits of IoT sensors in aircraft and GSE maintenance are too significant to ignore, making them an indispensable tool for modernizing and optimizing maintenance operations. As technology continues to evolve and mature, the role of IoT sensors in aviation maintenance is poised to expand, unlocking new opportunities for innovation and excellence in maintenance practices.
13. The Era of Customized Maintenance Plans for Aircraft and GSE
In the ever-evolving world of aviation maintenance, the one-size-fits-all approach is quickly becoming outdated. As aircraft fleets and ground support equipment (GSE) continue to diversify and evolve, maintenance strategies must adapt to meet the unique needs and operational requirements of each individual asset. Enter the era of customized maintenance plans, where maintenance software harnesses the power of data analytics and machine learning to generate tailored maintenance schedules based on individual usage patterns and operational conditions. In this blog post, we'll explore how customized maintenance plans are revolutionizing aircraft and GSE maintenance, leading to improved reliability, efficiency, and cost-effectiveness.
Traditionally, maintenance planning for aircraft and GSE has been based on fixed schedules or generic maintenance intervals determined by manufacturers or regulatory authorities. While these approaches provide a baseline for maintenance activities, they often fail to account for the specific operating conditions and usage patterns of individual assets. As a result, maintenance tasks may be performed too frequently, leading to unnecessary downtime and costs, or not frequently enough, increasing the risk of unexpected failures and safety incidents.
Customized maintenance plans address these shortcomings by leveraging data analytics and machine learning algorithms to analyze individual usage patterns and operational conditions for each asset. By collecting and analyzing data from onboard sensors, flight logs, maintenance records, and other sources, maintenance software can gain insights into how each asset is used, how it performs under different conditions, and what maintenance tasks are most critical to its reliability and safety.
One of the primary benefits of customized maintenance plans is their ability to optimize maintenance schedules based on actual usage patterns and operational conditions. For example, an aircraft that operates primarily in harsh environmental conditions or experiences frequent take-offs and landings may require more frequent inspections and maintenance tasks than an aircraft that operates in more benign conditions. By analyzing data on factors such as flight hours, cycles, and environmental conditions, maintenance software can generate customized maintenance schedules that ensure optimal performance and reliability while minimizing downtime and costs.
Moreover, customized maintenance plans enable maintenance organizations to prioritize maintenance tasks based on the criticality and impact of individual components and systems. By analyzing data on factors such as failure rates, mean time between failures (MTBF), and safety-criticality, maintenance software can identify the most critical components and systems that require immediate attention. This targeted approach to maintenance planning ensures that resources are allocated efficiently and effectively to address the most pressing maintenance needs, minimizing the risk of unexpected failures and safety incidents.
Furthermore, customized maintenance plans enable maintenance organizations to optimize their resources and reduce operational costs by avoiding unnecessary maintenance tasks and downtime. By tailoring maintenance schedules to the specific needs of each asset, maintenance software can identify opportunities to extend maintenance intervals for components and systems that are performing well and require less frequent attention. This proactive approach to maintenance planning helps to maximize asset utilization, minimize maintenance-related expenses, and improve overall operational efficiency.
In the realm of aircraft maintenance, customized maintenance plans offer unique capabilities for optimizing maintenance schedules and resource allocation for diverse fleets of aircraft. By analyzing data on factors such as aircraft usage, operating conditions, and component performance, maintenance software can generate customized maintenance schedules that ensure optimal reliability and safety while minimizing downtime and costs. These customized plans take into account the unique operating profiles of each aircraft, including factors such as flight routes, mission profiles, and environmental conditions, to tailor maintenance tasks to the specific needs of each asset.
Similarly, in GSE maintenance, customized maintenance plans provide valuable insights into the condition and performance of equipment such as baggage loaders, aircraft tugs, and ground power units. By analyzing data on factors such as equipment usage, duty cycles, and maintenance histories, maintenance software can generate customized maintenance schedules that optimize resource allocation and minimize downtime. These customized plans ensure that GSE remains operational and available when needed, while minimizing maintenance-related expenses and improving overall operational efficiency.
Despite their numerous advantages, the successful implementation of customized maintenance plans requires careful planning, data management, and integration with existing systems and processes. Maintenance organizations must ensure that they have access to high-quality, reliable data for training machine learning algorithms and generating customized maintenance schedules. Additionally, addressing concerns about data privacy, security, and regulatory compliance is essential to protect sensitive information and ensure compliance with industry regulations and standards.
In conclusion, customized maintenance plans are revolutionizing aircraft and GSE maintenance by leveraging data analytics and machine learning to generate tailored maintenance schedules based on individual usage patterns and operational conditions. By optimizing maintenance schedules, prioritizing critical tasks, and minimizing downtime and costs, customized maintenance plans help to improve reliability, efficiency, and cost-effectiveness in aviation maintenance operations. While challenges remain, the potential benefits of customized maintenance plans in aircraft and GSE maintenance are too significant to ignore, making them an indispensable tool for modernizing and optimizing maintenance operations. As technology continues to evolve and mature, the role of customized maintenance plans in aviation maintenance is poised to expand, unlocking new opportunities for innovation and excellence in maintenance practices.
14. The Future of Human-Machine Collaboration in Aircraft and GSE Maintenance
In the rapidly evolving landscape of aviation maintenance, the integration of advanced technologies such as artificial intelligence (AI) and automation is reshaping traditional practices. However, amid the rise of AI and automation, one fundamental truth remains unchanged: the indispensable role of human expertise. The future of maintenance will not be defined by machines alone but by a harmonious collaboration between skilled technicians and advanced technologies. In this blog post, we'll explore the evolving landscape of human-machine collaboration in aircraft and ground support equipment (GSE) maintenance, highlighting the vital role of both human expertise and technological innovation in ensuring comprehensive maintenance solutions.
As technology continues to advance, AI and automation are increasingly being integrated into aircraft and GSE maintenance operations. AI-powered predictive maintenance algorithms can analyze vast amounts of data to anticipate equipment failures and optimize maintenance schedules, while automated robotic systems can perform routine inspections and maintenance tasks with precision and efficiency. These technologies promise to revolutionize maintenance operations by improving reliability, reducing downtime, and optimizing resource allocation.
However, amid the rise of AI and automation, it's essential to recognize that human expertise remains indispensable in ensuring the safety, reliability, and effectiveness of maintenance operations. Skilled technicians bring a wealth of knowledge, experience, and intuition to the table – qualities that cannot be replicated by machines alone. From diagnosing complex issues to performing intricate repairs, human technicians play a crucial role in maintaining the airworthiness and operational integrity of aircraft and GSE.
The future of maintenance lies not in replacing humans with machines but in leveraging the strengths of both to achieve optimal outcomes. This requires a shift towards a collaborative approach to maintenance, where human technicians work hand-in-hand with advanced technologies to deliver comprehensive maintenance solutions. By combining the cognitive abilities of humans with the computational power of machines, maintenance organizations can achieve new levels of efficiency, reliability, and safety.
One of the key benefits of human-machine collaboration in maintenance is the ability to leverage the complementary strengths of humans and machines. While machines excel at processing large volumes of data and performing repetitive tasks with precision, humans possess cognitive abilities such as creativity, problem-solving, and adaptability. By harnessing the unique capabilities of both humans and machines, maintenance organizations can address a wider range of maintenance challenges and achieve better outcomes than either could alone.
Moreover, human-machine collaboration enables maintenance organizations to adapt and respond to changing conditions and requirements more effectively. In a dynamic and unpredictable operating environment, human technicians bring flexibility, intuition, and judgment to the table, enabling them to navigate unforeseen challenges and make informed decisions in real-time. By working collaboratively with advanced technologies, human technicians can leverage their expertise to overcome obstacles and optimize maintenance operations in response to changing circumstances.
Furthermore, human-machine collaboration fosters a culture of continuous learning and improvement within maintenance organizations. As technicians work alongside advanced technologies, they gain exposure to new tools, techniques, and methodologies that enhance their skills and capabilities. Likewise, machines learn from human interactions and feedback, enabling them to refine their algorithms and decision-making processes over time. This iterative process of learning and adaptation drives continuous improvement and innovation in maintenance practices and procedures.
In the realm of aircraft maintenance, human-machine collaboration enables technicians to perform a wide range of tasks more efficiently and effectively. For example, AI-powered diagnostic tools can assist technicians in troubleshooting complex issues by analyzing data from onboard sensors and systems, helping them identify root causes and develop targeted solutions. Similarly, automated robotic systems can assist technicians in performing routine inspections and maintenance tasks, freeing up their time to focus on more complex and critical activities.
Similarly, in GSE maintenance, human-machine collaboration enables technicians to optimize maintenance operations and improve equipment reliability. AI-powered predictive maintenance algorithms can analyze data from GSE sensors and systems to anticipate maintenance needs and prioritize tasks, while automated robotic systems can assist technicians in performing routine maintenance tasks with speed and precision. This collaborative approach to maintenance enables maintenance organizations to maximize equipment uptime, minimize downtime, and optimize resource allocation.
Despite the numerous benefits of human-machine collaboration in maintenance, challenges remain in integrating humans and machines effectively. One of the primary obstacles is ensuring seamless integration and interoperability between human technicians and advanced technologies. Maintenance organizations must invest in training and development programs to ensure that technicians have the skills and knowledge needed to work effectively alongside advanced technologies. Additionally, addressing concerns about job displacement and workforce readiness is essential to ensure a smooth transition to a collaborative maintenance model.
In conclusion, human-machine collaboration represents the future of maintenance in the aviation industry. By leveraging the complementary strengths of humans and machines, maintenance organizations can achieve new levels of efficiency, reliability, and safety in maintaining aircraft and ground support equipment. By fostering a culture of collaboration, continuous learning, and innovation, maintenance organizations can ensure that they remain at the forefront of technological advancements while preserving the invaluable expertise and experience of human technicians. As technology continues to evolve and mature, the potential benefits of human-machine collaboration in maintenance are limitless, making it an indispensable strategy for optimizing maintenance operations and ensuring the continued safety and reliability of aircraft and GSE.
15. The Era of Paperless Cockpits and GSE Control Centers in Aircraft Maintenance
In the ever-evolving world of aviation, where precision, safety, and efficiency are paramount, the digital revolution is transforming traditional practices. Among the many areas experiencing this transformation, aircraft maintenance and ground support equipment (GSE) maintenance are undergoing a significant shift towards paperless operations. Gone are the days of cumbersome paper manuals and logbooks; instead, the future heralds the dawn of paperless cockpits and GSE control centers. In this blog post, we'll explore how the digitization of maintenance manuals and paperwork is revolutionizing aircraft and GSE maintenance, enhancing safety, accuracy, and efficiency across the board.
The transition to paperless cockpits and GSE control centers represents a paradigm shift in how maintenance information is accessed, managed, and utilized. Traditionally, pilots, maintenance crews, and ground support personnel relied on printed manuals, checklists, and logbooks to perform their duties. However, this approach was not without its challenges, including the risk of errors, the burden of managing vast amounts of paperwork, and the inefficiencies associated with manual data entry and retrieval.
With the advent of digital technology, these challenges are being addressed through the digitization of maintenance manuals and paperwork. Maintenance manuals, checklists, and logbooks are being converted into digital formats, accessible via electronic flight bags (EFBs) in the cockpit and digital control centers on the ground. By digitizing maintenance documentation, pilots, maintenance crews, and ground support personnel can access all necessary information digitally, anytime, anywhere, with just a few taps or clicks.
One of the primary benefits of paperless cockpits and GSE control centers is the elimination of paper-based processes, resulting in reduced administrative burden and streamlined workflows. Instead of rifling through stacks of paper manuals and logbooks, pilots and maintenance crews can quickly search for and retrieve the information they need using intuitive digital interfaces. This not only saves time but also reduces the risk of errors associated with manual data entry and transcription.
Moreover, digital maintenance documentation enables real-time updates and revisions, ensuring that pilots, maintenance crews, and ground support personnel have access to the latest information at all times. Updates to maintenance procedures, regulations, or equipment specifications can be distributed instantly via digital channels, eliminating the need for manual distribution and ensuring that everyone is operating from the same page. This real-time access to accurate and up-to-date information enhances safety and compliance while minimizing the risk of outdated or obsolete documentation.
Furthermore, paperless cockpits and GSE control centers facilitate greater collaboration and communication among stakeholders involved in aircraft and GSE maintenance. Pilots, maintenance crews, and ground support personnel can share information and updates seamlessly via digital platforms, fostering a culture of collaboration and teamwork. For example, if a maintenance issue arises during a flight, pilots can communicate with maintenance crews on the ground in real-time, sharing relevant information and coordinating the necessary actions to resolve the issue promptly.
In the realm of aircraft maintenance, paperless cockpits enable pilots to access critical maintenance information and procedures directly from their EFBs, eliminating the need for bulky paper manuals and checklists. Pre-flight and post-flight checks can be performed more efficiently, with digital checklists guiding pilots through each step of the process. Additionally, digital maintenance logs allow pilots to record and track maintenance activities in real-time, providing a comprehensive record of maintenance history and compliance.
Similarly, in GSE maintenance, digital control centers provide ground support personnel with centralized access to maintenance documentation and procedures for GSE such as baggage loaders, aircraft tugs, and ground power units. Maintenance tasks can be planned, scheduled, and tracked digitally, with real-time updates and notifications alerting personnel to maintenance needs or issues. This centralized approach to GSE maintenance improves coordination, efficiency, and visibility into maintenance operations.
Despite the numerous benefits of paperless cockpits and GSE control centers, challenges remain in the transition to digital maintenance documentation. One of the primary obstacles is ensuring data security and integrity, particularly in the aviation industry, where safety and compliance are paramount. Maintenance organizations must implement robust cybersecurity measures to protect digital maintenance documentation from unauthorized access, tampering, or loss. Additionally, addressing concerns about data privacy, regulatory compliance, and interoperability with existing systems is essential to ensure a smooth transition to paperless operations.
In conclusion, paperless cockpits and GSE control centers represent the future of aircraft and GSE maintenance, enabling pilots, maintenance crews, and ground support personnel to access critical maintenance information digitally, anytime, anywhere. By eliminating paper-based processes and streamlining workflows, digital maintenance documentation enhances safety, accuracy, and efficiency across the board. While challenges remain in the transition to paperless operations, the potential benefits are too significant to ignore, making it an indispensable strategy for modernizing and optimizing maintenance operations in the aviation industry. As technology continues to evolve and mature, the role of paperless cockpits and GSE control centers in aircraft and GSE maintenance is poised to expand, unlocking new opportunities for innovation and excellence in maintenance practices.
16. Environmental Impact Considerations in Aircraft and GSE Maintenance
In an era defined by increasing environmental consciousness and sustainability efforts, industries across the globe are reevaluating their practices to minimize their ecological footprint. The aviation sector, with its significant impact on the environment, is no exception. As aircraft fleets and ground support equipment (GSE) continue to grow, maintenance practices are evolving to prioritize not only mechanical efficiency but also environmental impact. In this blog post, we'll explore how aircraft and GSE maintenance software are embracing sustainable practices and green technologies to minimize environmental harm and pave the way towards a greener future.
Historically, aircraft and GSE maintenance has focused primarily on ensuring mechanical efficiency, reliability, and safety. However, as concerns about climate change and environmental degradation mount, there is a growing recognition that maintenance practices must also consider their environmental impact. From reducing carbon emissions to minimizing waste and pollution, there are numerous opportunities for the aviation industry to embrace sustainability and adopt green technologies in maintenance operations.
One of the key ways in which aircraft and GSE maintenance software can contribute to environmental sustainability is by optimizing maintenance schedules and procedures to minimize fuel consumption and emissions. By analyzing data on factors such as flight patterns, engine performance, and operational efficiency, maintenance software can identify opportunities to reduce fuel burn and emissions through more efficient maintenance practices. For example, by optimizing engine maintenance schedules to ensure peak performance and efficiency, airlines can reduce fuel consumption and greenhouse gas emissions during flight operations.
Moreover, aircraft and GSE maintenance software can play a crucial role in promoting the use of sustainable materials and technologies in maintenance operations. From lightweight composite materials to electric and hybrid propulsion systems, there are numerous green technologies available that can help reduce the environmental impact of aircraft and GSE. Maintenance software can help maintenance organizations identify and implement these technologies by providing data-driven insights into their performance, reliability, and cost-effectiveness.
Furthermore, aircraft and GSE maintenance software can facilitate the adoption of sustainable practices such as waste reduction, recycling, and energy efficiency in maintenance operations. By digitizing maintenance documentation and procedures, maintenance software can reduce paper usage and waste, while also streamlining workflows and minimizing resource consumption. Additionally, by leveraging predictive analytics and machine learning algorithms, maintenance software can optimize resource allocation and minimize energy usage in maintenance facilities, leading to further reductions in environmental impact.
In the realm of aircraft maintenance, environmental impact considerations are driving the adoption of sustainable practices and green technologies across all aspects of maintenance operations. From airframe maintenance to engine overhauls, maintenance organizations are exploring innovative solutions to minimize environmental harm and promote sustainability. For example, the use of lightweight composite materials in aircraft construction can reduce fuel consumption and emissions, while the adoption of electric and hybrid propulsion systems can further reduce the environmental impact of aircraft operations.
Similarly, in GSE maintenance, environmental impact considerations are driving the adoption of sustainable practices and technologies to minimize emissions and pollution. From electric baggage loaders to hybrid aircraft tugs, there are numerous green technologies available that can help reduce the environmental impact of GSE operations. Maintenance organizations are increasingly embracing these technologies to promote sustainability and reduce their ecological footprint.
Despite the numerous benefits of incorporating environmental impact considerations into aircraft and GSE maintenance, challenges remain in implementing sustainable practices and technologies. One of the primary obstacles is the cost associated with adopting green technologies and implementing sustainable practices. While the long-term benefits of sustainability are clear, the upfront costs of investing in new technologies and infrastructure can be prohibitive for some maintenance organizations.
In conclusion, environmental impact considerations are reshaping the landscape of aircraft and GSE maintenance, driving the adoption of sustainable practices and green technologies across all aspects of maintenance operations. From optimizing maintenance schedules to promoting the use of sustainable materials and technologies, maintenance organizations are embracing sustainability as a core principle of their operations. While challenges remain, the potential benefits of prioritizing environmental impact considerations in maintenance operations are significant, making it an indispensable strategy for promoting sustainability and mitigating the environmental impact of aviation operations. As technology continues to evolve and mature, the role of aircraft and GSE maintenance software in driving environmental sustainability is poised to expand, unlocking new opportunities for innovation and excellence in maintenance practices.
17. Rapid Data Analysis for Aircraft and GSE
In the dynamic world of aviation maintenance, time is of the essence. Every moment counts when it comes to ensuring the safety, reliability, and efficiency of both aircraft and ground support equipment (GSE). As the industry continues to embrace digital transformation, the power of big data analytics is revolutionizing maintenance operations, providing maintenance crews with rapid insights and actionable information. In this blog post, we'll explore how rapid data analysis is reshaping aircraft and GSE maintenance, empowering maintenance crews to make informed decisions swiftly and effectively.
Traditionally, maintenance operations relied on manual data collection and analysis, a time-consuming and labor-intensive process that often resulted in delays and inefficiencies. However, with the advent of big data analytics, maintenance organizations now have access to powerful tools and technologies that can process vast amounts of data in real-time, providing rapid insights into the health and performance of aircraft and GSE.
One of the primary benefits of rapid data analysis in aircraft and GSE maintenance is the ability to detect and diagnose issues quickly and accurately. By analyzing data from onboard sensors, flight logs, maintenance records, and other sources, maintenance software can identify anomalies and trends that may indicate potential issues or areas of concern. Maintenance crews can then receive real-time alerts and notifications, enabling them to investigate the issue further and take corrective action promptly.
Moreover, rapid data analysis enables maintenance crews to prioritize maintenance tasks and allocate resources more effectively. By identifying critical issues and predicting potential failures in advance, maintenance software can help maintenance crews focus their efforts on the most pressing maintenance needs, minimizing downtime and maximizing operational efficiency. This targeted approach to maintenance planning ensures that resources are allocated where they are needed most, optimizing the overall effectiveness of maintenance operations.
Furthermore, rapid data analysis facilitates data-driven decision-making in maintenance operations, enabling maintenance crews to make informed decisions based on real-time insights and actionable information. By providing maintenance crews with access to up-to-date information and performance metrics, maintenance software empowers them to assess the situation quickly, evaluate various options, and choose the most appropriate course of action. This data-driven approach to decision-making helps maintenance crews respond swiftly and effectively to maintenance needs, minimizing disruptions and maximizing aircraft and GSE availability.
In the realm of aircraft maintenance, rapid data analysis is transforming how maintenance tasks are planned, executed, and monitored. From pre-flight checks to post-flight inspections, maintenance crews rely on real-time data analysis to ensure the airworthiness and operational integrity of aircraft. For example, by analyzing data from aircraft sensors and systems, maintenance software can detect anomalies and trends that may indicate potential issues with critical components such as engines, avionics systems, and structural elements. Maintenance crews can then receive alerts and notifications in real-time, enabling them to address the issue promptly and prevent further damage or degradation.
Similarly, in GSE maintenance, rapid data analysis plays a crucial role in optimizing maintenance operations and maximizing equipment uptime. From baggage loaders to aircraft tugs, GSE maintenance crews rely on real-time data analysis to monitor the health and performance of equipment and identify maintenance needs proactively. By analyzing data from GSE sensors and systems, maintenance software can detect anomalies and trends that may indicate potential issues with components such as engines, hydraulics, and electronics. Maintenance crews can then take corrective action promptly, minimizing downtime and ensuring that GSE remains operational and available when needed.
Despite the numerous benefits of rapid data analysis in aircraft and GSE maintenance, challenges remain in implementing and leveraging these technologies effectively. One of the primary obstacles is ensuring data quality and integrity, particularly in an industry where safety and reliability are paramount. Maintenance organizations must invest in robust data management practices and technologies to ensure that data is accurate, reliable, and secure. Additionally, addressing concerns about data privacy, regulatory compliance, and interoperability with existing systems is essential to ensure a smooth transition to rapid data analysis in maintenance operations.
In conclusion, rapid data analysis is revolutionizing aircraft and GSE maintenance, providing maintenance crews with real-time insights and actionable information that enable them to make informed decisions swiftly and effectively. By leveraging the power of big data analytics, maintenance organizations can detect and diagnose issues quickly, prioritize maintenance tasks more effectively, and optimize resource allocation to maximize operational efficiency. While challenges remain, the potential benefits of rapid data analysis in aircraft and GSE maintenance are too significant to ignore, making it an indispensable tool for modernizing and optimizing maintenance operations in the aviation industry. As technology continues to evolve and mature, the role of rapid data analysis in aircraft and GSE maintenance is poised to expand, unlocking new opportunities for innovation and excellence in maintenance practices.
18. Remote Troubleshooting for Aircraft and GSE Maintenance
In the realm of aircraft and ground support equipment (GSE) maintenance, efficiency is paramount. Every moment an aircraft or a piece of equipment is out of service for maintenance translates into potential delays and increased operational costs. To address this challenge, the industry is embracing innovative solutions that allow for remote troubleshooting, minimizing downtime and maximizing efficiency. Remote diagnostic tools, coupled with augmented reality interfaces, are revolutionizing the way maintenance technicians identify and address issues, ensuring optimal performance for both aircraft and GSE. In this blog post, we'll delve into the world of remote troubleshooting and explore how it is reshaping maintenance practices in the aviation industry.
Traditionally, troubleshooting maintenance issues required technicians to be physically present at the aircraft or equipment site, which often led to delays as technicians traveled to the location. However, with advancements in technology, remote troubleshooting has emerged as a game-changer. Remote diagnostic tools leverage real-time data streaming and augmented reality interfaces to allow experts to guide on-site personnel through repairs and maintenance tasks from anywhere in the world.
One of the primary benefits of remote troubleshooting is the ability to address maintenance issues promptly, regardless of the technician's location. By accessing real-time data streams from sensors and onboard systems, experts can remotely monitor the health and performance of aircraft and GSE, identifying potential issues before they escalate into major problems. With augmented reality interfaces, experts can provide step-by-step guidance to on-site personnel, facilitating efficient troubleshooting and minimizing downtime.
Moreover, remote troubleshooting enables maintenance organizations to leverage the expertise of specialized technicians and engineers more effectively. Rather than dispatching technicians to every maintenance site, organizations can centralize their experts in a control center or hub, where they can remotely monitor and troubleshoot maintenance issues for multiple aircraft or pieces of equipment simultaneously. This centralized approach allows organizations to optimize resource allocation and ensure that the right expertise is available when and where it's needed most.
Furthermore, remote troubleshooting enhances collaboration and knowledge sharing among maintenance teams. By providing real-time access to experts and specialists, augmented reality interfaces enable on-site personnel to learn from experienced technicians and gain valuable insights into maintenance best practices. This collaborative approach fosters a culture of continuous learning and improvement, empowering maintenance teams to enhance their skills and capabilities over time.
In the realm of aircraft maintenance, remote troubleshooting is revolutionizing how maintenance tasks are performed and managed. From diagnosing avionics issues to troubleshooting engine problems, experts can remotely access onboard systems and sensors to monitor aircraft health and performance in real-time. Augmented reality interfaces provide on-site technicians with visual cues and instructions, guiding them through complex repair procedures with precision and efficiency.
Similarly, in GSE maintenance, remote troubleshooting is streamlining maintenance operations and maximizing equipment uptime. From diagnosing electrical faults to troubleshooting hydraulic systems, experts can remotely monitor GSE health and performance, identifying potential issues and providing guidance to on-site personnel as needed. Augmented reality interfaces enable technicians to visualize equipment components and systems in real-time, facilitating efficient troubleshooting and repair.
Despite the numerous benefits of remote troubleshooting, challenges remain in implementing and leveraging these technologies effectively. One of the primary obstacles is ensuring reliable connectivity and data transmission, particularly in remote or challenging environments. Maintenance organizations must invest in robust communication infrastructure and cybersecurity measures to ensure that remote troubleshooting tools function reliably and securely. Additionally, addressing concerns about data privacy, regulatory compliance, and interoperability with existing systems is essential to ensure a smooth transition to remote troubleshooting in maintenance operations.
In conclusion, remote troubleshooting is transforming aircraft and GSE maintenance, enabling organizations to address maintenance issues promptly and efficiently from anywhere in the world. By leveraging real-time data streaming and augmented reality interfaces, maintenance teams can diagnose problems, perform repairs, and optimize maintenance operations with unprecedented speed and accuracy. While challenges remain, the potential benefits of remote troubleshooting in aircraft and GSE maintenance are too significant to ignore, making it an indispensable tool for modernizing and optimizing maintenance operations in the aviation industry. As technology continues to evolve and mature, the role of remote troubleshooting in aircraft and GSE maintenance is poised to expand, unlocking new opportunities for innovation and excellence in maintenance practices.
19. Embracing Predictability: Subscription-Based Models for Aircraft and GSE Maintenance Services
In the ever-evolving landscape of aircraft and ground support equipment (GSE) maintenance, predictability and cost-effectiveness are essential factors that drive operational efficiency and sustainability. To address the challenges associated with maintenance budgeting and planning, the aviation industry is witnessing a paradigm shift towards subscription-based models for maintenance services. These models offer airlines and ground support service providers a predictable and transparent framework for managing maintenance costs, ensuring optimal performance for both aircraft and GSE. In this blog post, we'll explore how subscription-based models are reshaping maintenance practices in the aviation industry and the benefits they offer for airlines and ground support service providers alike.
Traditionally, maintenance costs have been a significant source of uncertainty for airlines and ground support service providers. Unforeseen maintenance issues and unexpected expenses can disrupt budgeting and planning efforts, leading to financial strain and operational inefficiencies. However, with the advent of subscription-based models for maintenance services, organizations can now enjoy greater predictability and transparency in their maintenance costs. One of the primary benefits of subscription-based models is the predictability they offer in maintenance costs. Rather than dealing with unpredictable and fluctuating expenses, airlines and ground support service providers can subscribe to a maintenance plan that provides a fixed monthly or annual fee for a predetermined set of services. This predictable pricing structure allows organizations to budget more effectively for maintenance expenses, eliminating the uncertainty associated with traditional pay-as-you-go models.
Moreover, subscription-based models enable organizations to tailor maintenance plans to their specific needs and requirements. Airlines and ground support service providers can choose from a range of subscription options based on factors such as fleet size, aircraft type, and operational profile. This flexibility allows organizations to select the level of coverage and support that best aligns with their operational priorities and budget constraints, ensuring that they receive the services they need at a price they can afford.
Furthermore, subscription-based models promote a proactive approach to maintenance, rather than a reactive one. By subscribing to a maintenance plan, organizations can access preventive maintenance services and proactive support measures designed to minimize the risk of unexpected failures and downtime. This proactive approach helps organizations identify and address potential issues before they escalate into major problems, reducing the likelihood of costly repairs and disruptions to operations. In the realm of aircraft maintenance, subscription-based models offer airlines a comprehensive solution for managing the maintenance needs of their fleets. Rather than relying on ad-hoc maintenance services and pay-as-you-go arrangements, airlines can subscribe to a maintenance plan that covers everything from routine inspections to major overhauls. This all-inclusive approach ensures that airlines receive the support and services they need to keep their aircraft flying safely and reliably, without having to worry about unexpected maintenance expenses.
Similarly, in GSE maintenance, subscription-based models provide ground support service providers with a cost-effective and efficient solution for managing the maintenance needs of their equipment fleets. By subscribing to a maintenance plan, service providers can access a range of services and support measures designed to keep their equipment operating at peak performance. From routine maintenance tasks to emergency repairs, subscription-based models offer service providers the flexibility and peace of mind they need to manage their maintenance operations effectively.
Despite the numerous benefits of subscription-based models, challenges remain in implementing and adopting these models effectively. One of the primary obstacles is ensuring alignment between the services offered under the subscription plan and the actual maintenance needs of the organization. Maintenance organizations must work closely with their service providers to define clear service level agreements (SLAs) and performance metrics to ensure that the subscription plan meets their operational requirements.
In conclusion, subscription-based models are revolutionizing aircraft and GSE maintenance, offering airlines and ground support service providers a predictable, transparent, and cost-effective framework for managing maintenance costs. By providing a fixed pricing structure, tailored service options, and proactive support measures, subscription-based models enable organizations to budget more effectively for maintenance expenses, reduce the risk of unexpected failures and downtime, and optimize the performance of their aircraft and GSE fleets. While challenges remain, the potential benefits of subscription-based models in aircraft and GSE maintenance are too significant to ignore, making them an indispensable tool for modernizing and optimizing maintenance operations in the aviation industry. As organizations continue to embrace these models, the future of maintenance promises to be more predictable, efficient, and sustainable than ever before.
20. Embracing Open-Source Collaboration in Aircraft and GSE Maintenance
In the ever-evolving realm of aircraft and ground support equipment (GSE) maintenance, collaboration and innovation are essential drivers of progress. As the aviation industry continues to embrace digital transformation, there is a growing recognition of the benefits of open-source collaboration in developing maintenance software for both aircraft and GSE. By sharing knowledge, resources, and technology, the aviation community can foster faster innovation, drive industry-wide improvements, and ultimately enhance safety, reliability, and efficiency across the board. In this blog post, we'll explore the concept of open-source collaboration in maintenance software and its potential to revolutionize maintenance practices in the aviation industry.
Traditionally, the development of maintenance software for aircraft and GSE has been dominated by proprietary solutions developed by individual companies or manufacturers. While these solutions have served their purpose, they often come with limitations such as high costs, vendor lock-in, and lack of interoperability. Moreover, the pace of innovation in the industry has been hampered by the siloed nature of development, with limited collaboration and knowledge sharing among stakeholders.
Open-source collaboration offers a solution to these challenges by promoting transparency, inclusivity, and community-driven development. By sharing code, best practices, and resources openly, the aviation community can leverage the collective expertise and creativity of a diverse range of contributors, including airlines, maintenance organizations, manufacturers, and software developers. This collaborative approach encourages innovation, accelerates the development cycle, and ensures that maintenance software remains up-to-date, relevant, and adaptable to evolving needs and requirements.
One of the primary benefits of open-source collaboration in aircraft and GSE maintenance is the democratization of technology. By making maintenance software accessible to a wider audience, regardless of size or resources, open-source collaboration enables smaller operators and organizations to leverage advanced technology and best practices that were previously out of reach. This levels the playing field and fosters greater competition, innovation, and efficiency in the industry.
Moreover, open-source collaboration promotes interoperability and compatibility among different systems and platforms. By adopting open standards and protocols, maintenance software developed through open-source collaboration can seamlessly integrate with existing systems and infrastructure, eliminating the need for costly customizations and proprietary interfaces. This interoperability enhances flexibility, scalability, and efficiency, allowing organizations to leverage their existing investments while embracing new technologies and solutions.
Furthermore, open-source collaboration fosters a culture of transparency and trust within the aviation community. By openly sharing code, documentation, and contributions, developers and organizations can collaborate more effectively, identify and address issues collectively, and build consensus around common goals and priorities. This transparency not only promotes accountability and quality assurance but also fosters a sense of ownership and pride among contributors, driving greater engagement and participation in the development process.
In the realm of aircraft maintenance, open-source collaboration is revolutionizing how maintenance software is developed, deployed, and utilized. From aircraft health monitoring to maintenance planning and scheduling, open-source solutions offer a range of tools and capabilities that empower maintenance organizations to optimize their operations and maximize aircraft availability. By providing access to a rich ecosystem of modules, plugins, and extensions, open-source collaboration enables organizations to customize and extend their maintenance software to meet their specific needs and requirements.
Similarly, in GSE maintenance, open-source collaboration is driving innovation and efficiency in maintenance operations. From fleet management to equipment diagnostics and repair, open-source solutions offer a comprehensive suite of tools and features that enable ground support service providers to streamline their operations and minimize downtime. By leveraging open-source platforms and frameworks, organizations can develop tailored solutions that integrate seamlessly with their existing systems and workflows, enhancing productivity, reliability, and cost-effectiveness.
Despite the numerous benefits of open-source collaboration, challenges remain in implementing and adopting these principles effectively. One of the primary obstacles is overcoming cultural barriers and resistance to change within the industry. Many organizations may be hesitant to embrace open-source collaboration due to concerns about intellectual property rights, security, and control. However, by fostering a culture of openness, collaboration, and knowledge sharing, the aviation community can overcome these challenges and unlock the full potential of open-source development.
In conclusion, open-source collaboration holds immense promise for revolutionizing aircraft and GSE maintenance, offering a collaborative, inclusive, and community-driven approach to software development. By sharing knowledge, resources, and technology openly, the aviation community can drive faster innovation, foster industry-wide improvements, and enhance safety, reliability, and efficiency across the board. While challenges remain, the potential benefits of open-source collaboration in maintenance software are too significant to ignore, making it an indispensable tool for modernizing and optimizing maintenance practices in the aviation industry. As organizations continue to embrace open-source principles, the future of maintenance promises to be more collaborative, innovative, and inclusive than ever before.
21. Real-Time Health Monitoring for Aircraft and GSE
In the fast-paced world of aviation, safety, reliability, and efficiency are paramount. The ability to detect and address potential issues before they escalate into major problems is critical to ensuring the smooth operation of both aircraft and ground support equipment (GSE). To meet this challenge, the aviation industry is increasingly turning to real-time health monitoring systems that provide continuous oversight of aircraft and GSE systems. By monitoring key parameters in real-time and triggering immediate alerts in the event of deviations from optimal conditions, these systems enable proactive maintenance measures that enhance safety, reliability, and efficiency across the board. In this blog post, we'll explore the concept of real-time health monitoring for aircraft and GSE and its potential to revolutionize maintenance practices in the aviation industry.
Traditionally, maintenance operations for aircraft and GSE have relied on periodic inspections and scheduled maintenance tasks to ensure their continued airworthiness and operational integrity. While these methods have served their purpose, they have limitations in terms of their ability to detect and address issues in real-time. In today's fast-paced aviation environment, where every minute counts, there is a growing need for a more proactive approach to maintenance that enables organizations to identify and address potential issues as soon as they arise.
Real-time health monitoring systems offer a solution to this challenge by providing continuous oversight of aircraft and GSE systems, allowing organizations to monitor key parameters such as engine performance, avionics systems, and structural integrity in real-time. These systems leverage onboard sensors, data acquisition systems, and advanced analytics algorithms to collect, analyze, and interpret data from various sources, providing maintenance crews with timely insights into the health and performance of aircraft and GSE.
One of the primary benefits of real-time health monitoring is the ability to detect and diagnose issues as soon as they occur, enabling maintenance crews to take immediate action to address them. By monitoring key parameters such as temperature, pressure, vibration, and fluid levels in real-time, these systems can identify deviations from optimal conditions that may indicate potential issues or areas of concern. Immediate alerts can then be triggered, notifying maintenance crews of the problem and enabling them to investigate further and take corrective action promptly.
Moreover, real-time health monitoring systems enable organizations to implement proactive maintenance measures that help prevent issues from escalating into major problems. By identifying potential issues in their early stages, maintenance crews can take preventive action to address them before they lead to costly repairs, downtime, or safety incidents. This proactive approach to maintenance helps organizations minimize disruptions to operations, maximize equipment uptime, and enhance safety and reliability across the board.
Furthermore, real-time health monitoring systems provide maintenance crews with actionable insights and recommendations for optimizing performance and efficiency. By analyzing data trends and patterns over time, these systems can identify opportunities for improving maintenance practices, optimizing operational parameters, and enhancing equipment performance. Maintenance crews can then use this information to make informed decisions about maintenance tasks, scheduling, and resource allocation, ensuring that maintenance operations are conducted in the most efficient and cost-effective manner possible.
In the realm of aircraft maintenance, real-time health monitoring systems are revolutionizing how maintenance tasks are planned, executed, and monitored. From engine health monitoring to avionics diagnostics and structural integrity assessments, these systems provide maintenance crews with a comprehensive suite of tools and capabilities for monitoring and managing the health and performance of aircraft systems in real-time. By leveraging real-time data and analytics, maintenance crews can identify potential issues before they escalate into major problems, enabling them to conduct timely repairs, replacements, or adjustments as needed.
Similarly, in GSE maintenance, real-time health monitoring systems are driving innovation and efficiency in maintenance operations. From engine diagnostics to hydraulic system monitoring and electrical system health checks, these systems provide ground support service providers with the tools and capabilities they need to monitor and manage the health and performance of GSE systems in real-time. By leveraging real-time data and analytics, service providers can identify potential issues early on, enabling them to take preventive action to address them before they lead to costly repairs or downtime.
Despite the numerous benefits of real-time health monitoring, challenges remain in implementing and adopting these systems effectively. One of the primary obstacles is ensuring reliable connectivity and data transmission, particularly in remote or challenging environments. Maintenance organizations must invest in robust communication infrastructure and cybersecurity measures to ensure that real-time health monitoring systems function reliably and securely. Additionally, addressing concerns about data privacy, regulatory compliance, and interoperability with existing systems is essential to ensure a smooth transition to real-time health monitoring in maintenance operations.
In conclusion, real-time health monitoring systems are revolutionizing aircraft and GSE maintenance, providing organizations with the tools and capabilities they need to monitor and manage the health and performance of their assets in real-time. By providing continuous oversight of key parameters and triggering immediate alerts in the event of deviations from optimal conditions, these systems enable proactive maintenance measures that enhance safety, reliability, and efficiency across the board. While challenges remain, the potential benefits of real-time health monitoring in aircraft and GSE maintenance are too significant to ignore, making it an indispensable tool for modernizing and optimizing maintenance practices in the aviation industry. As organizations continue to embrace real-time health monitoring, the future of maintenance promises to be more proactive, efficient, and effective than ever before.
22. The Role of Global Connectivity in Aircraft and GSE Maintenance
In today's interconnected world, communication and collaboration are fundamental to the success of any endeavor, and the aviation industry is no exception. As aircraft and ground support equipment (GSE) become increasingly complex, the need for seamless coordination and real-time information sharing between stakeholders has never been greater. To address this challenge, the aviation community is embracing global connectivity in maintenance software, enabling real-time communication and collaboration between different stakeholders, from manufacturers to maintenance crews. In this blog post, we'll explore the concept of global connectivity in aircraft and GSE maintenance and its potential to revolutionize maintenance practices in the aviation industry.
Traditionally, maintenance operations for aircraft and GSE have been fragmented and siloed, with limited communication and collaboration between different stakeholders. Manufacturers, airlines, maintenance organizations, and regulatory authorities each have their own systems and processes for managing maintenance activities, often resulting in inefficiencies, delays, and miscommunication. However, with the advent of global connectivity in maintenance software, these barriers are being broken down, enabling seamless communication and collaboration across the entire maintenance ecosystem.
One of the primary benefits of global connectivity in aircraft and GSE maintenance is the ability to share real-time information and data between different stakeholders. By connecting maintenance software systems globally, manufacturers can provide airlines and maintenance organizations with access to real-time data on aircraft and GSE performance, maintenance history, and technical documentation. This real-time information sharing enables stakeholders to make informed decisions about maintenance planning, scheduling, and execution, ensuring that maintenance activities are conducted efficiently and effectively.
Moreover, global connectivity enables stakeholders to collaborate more effectively on maintenance tasks and projects. By providing real-time communication channels and collaboration tools, maintenance software systems allow manufacturers, airlines, and maintenance organizations to work together seamlessly on maintenance activities, such as troubleshooting complex issues, coordinating maintenance tasks, and sharing best practices. This collaborative approach fosters a culture of teamwork and innovation, driving continuous improvement and excellence in maintenance practices.
Furthermore, global connectivity enhances transparency and accountability in aircraft and GSE maintenance. By providing stakeholders with visibility into maintenance activities and processes, maintenance software systems enable manufacturers, airlines, and maintenance organizations to track the progress of maintenance tasks, monitor compliance with regulations and standards, and identify areas for improvement. This transparency promotes accountability and quality assurance, ensuring that maintenance activities are conducted in accordance with industry best practices and regulatory requirements.
In the realm of aircraft maintenance, global connectivity is revolutionizing how maintenance tasks are planned, executed, and monitored. From pre-flight checks to post-flight inspections, maintenance crews rely on real-time data and communication channels to ensure the airworthiness and operational integrity of aircraft. By connecting maintenance software systems globally, airlines and maintenance organizations can access real-time information on aircraft performance and maintenance history, enabling them to make informed decisions about maintenance activities and prioritize tasks based on criticality and urgency.
Similarly, in GSE maintenance, global connectivity is driving efficiency and effectiveness in maintenance operations. From equipment diagnostics to repair and overhaul, ground support service providers rely on real-time communication and collaboration tools to ensure the reliability and availability of GSE. By connecting maintenance software systems globally, service providers can access real-time data on GSE performance and maintenance history, enabling them to identify potential issues and take proactive action to address them before they escalate into major problems.
Despite the numerous benefits of global connectivity, challenges remain in implementing and adopting these systems effectively. One of the primary obstacles is ensuring reliable connectivity and data transmission, particularly in remote or challenging environments. Maintenance organizations must invest in robust communication infrastructure and cybersecurity measures to ensure that global connectivity systems function reliably and securely. Additionally, addressing concerns about data privacy, regulatory compliance, and interoperability with existing systems is essential to ensure a smooth transition to global connectivity in maintenance operations.
In conclusion, global connectivity is transforming aircraft and GSE maintenance, enabling stakeholders to share real-time information, collaborate effectively, and drive continuous improvement in maintenance practices. By connecting maintenance software systems globally, manufacturers, airlines, and maintenance organizations can work together seamlessly to ensure the safety, reliability, and efficiency of aircraft and GSE. While challenges remain, the potential benefits of global connectivity in maintenance are too significant to ignore, making it an indispensable tool for modernizing and optimizing maintenance practices in the aviation industry. As organizations continue to embrace global connectivity, the future of maintenance promises to be more connected, collaborative, and efficient than ever before.
23. Enhanced Training Simulators for Aircraft and GSE Maintenance
In the dynamic world of aviation, where safety and precision are paramount, the importance of well-trained maintenance personnel cannot be overstated. The ability of technicians to effectively diagnose and address issues with aircraft and ground support equipment (GSE) is crucial to ensuring the reliability and safety of aviation operations. To meet the demands of an ever-evolving industry, training methodologies must evolve as well. Enter enhanced training simulators, leveraging virtual reality (VR) and augmented reality (AR) technologies to provide maintenance personnel with immersive and realistic training scenarios. In this blog post, we'll delve into the realm of enhanced training simulators for aircraft and GSE maintenance, exploring how VR and AR are transforming training practices and enhancing the skills of maintenance personnel.
Traditionally, training for aircraft and GSE maintenance has relied on a combination of classroom instruction, hands-on experience, and simulation-based training. While these methods have proven effective to some extent, they often come with limitations such as cost, accessibility, and scalability. Enhanced training simulators aim to overcome these challenges by providing maintenance personnel with immersive, interactive, and realistic training experiences that closely mimic real-world scenarios.
One of the primary benefits of enhanced training simulators is the ability to provide maintenance personnel with hands-on experience in a safe and controlled environment. By leveraging VR and AR technologies, these simulators can recreate complex maintenance tasks and scenarios with unprecedented realism, allowing technicians to practice and refine their skills without putting themselves or others at risk. From engine diagnostics to avionics troubleshooting, maintenance personnel can immerse themselves in a virtual environment that closely mirrors the challenges they may encounter in the field.
Moreover, enhanced training simulators offer a level of flexibility and scalability that traditional training methods cannot match. By providing access to virtual training environments that can be accessed anytime, anywhere, maintenance personnel can engage in training activities at their own pace and convenience, without the need for specialized equipment or dedicated training facilities. This accessibility makes it easier for organizations to provide ongoing training and professional development opportunities for their maintenance personnel, ensuring that their skills remain up-to-date and relevant in an ever-changing industry landscape.
Furthermore, enhanced training simulators enable organizations to simulate a wide range of scenarios and conditions that may be difficult or impossible to replicate in real-world training environments. By leveraging VR and AR technologies, these simulators can recreate challenging weather conditions, equipment malfunctions, and emergency situations with unparalleled realism, providing maintenance personnel with valuable experience and exposure to scenarios they may encounter in their day-to-day work. This realistic training helps prepare technicians to respond effectively and confidently to unexpected challenges, minimizing the risk of errors and ensuring the safety and reliability of aviation operations.
In the realm of aircraft maintenance, enhanced training simulators are revolutionizing how maintenance personnel are trained and prepared for their roles. From engine maintenance to structural repairs, technicians can engage in virtual training scenarios that closely mimic the challenges they may encounter in the field. By providing hands-on experience in a virtual environment, these simulators enable technicians to practice and refine their skills in a safe and controlled setting, ensuring that they are well-equipped to perform their duties with precision and confidence.
Similarly, in GSE maintenance, enhanced training simulators are driving innovation and efficiency in training operations. From equipment diagnostics to routine maintenance tasks, technicians can engage in virtual training exercises that simulate the operation and maintenance of various types of GSE. By providing a realistic and immersive training experience, these simulators enable technicians to develop the skills and expertise they need to keep GSE operating at peak performance, minimizing downtime and maximizing efficiency.
Despite the numerous benefits of enhanced training simulators, challenges remain in implementing and adopting these technologies effectively. One of the primary obstacles is ensuring that simulators accurately replicate real-world scenarios and conditions, providing maintenance personnel with a realistic and immersive training experience. Additionally, addressing concerns about cost, accessibility, and training effectiveness is essential to ensure that enhanced training simulators deliver tangible benefits to organizations and their maintenance personnel.
In conclusion, enhanced training simulators are revolutionizing aircraft and GSE maintenance, providing maintenance personnel with immersive, interactive, and realistic training experiences that enable them to develop and refine their skills with unprecedented precision and confidence. By leveraging VR and AR technologies, these simulators offer a level of realism and flexibility that traditional training methods cannot match, empowering technicians to respond effectively to the challenges they may encounter in the field. While challenges remain, the potential benefits of enhanced training simulators in aircraft and GSE maintenance are too significant to ignore, making them an indispensable tool for modernizing and optimizing training practices in the aviation industry. As organizations continue to embrace these technologies, the future of maintenance training promises to be more immersive, interactive, and effective than ever before.
24. Streamlining Compliance: The Role of Automation in Aircraft and GSE Maintenance
In the ever-evolving landscape of aviation, regulatory compliance is a cornerstone of safety and reliability. Adhering to stringent regulations ensures that aircraft and ground support equipment (GSE) are maintained to the highest standards, minimizing the risk of accidents and ensuring the smooth operation of aviation activities. However, keeping up with evolving regulations can be a daunting task for maintenance personnel and organizations. Enter regulatory compliance automation, a transformative approach that leverages technology to ensure seamless adherence to aviation standards. In this blog post, we'll explore the concept of regulatory compliance automation for aircraft and GSE maintenance, and how it's poised to revolutionize maintenance practices in the aviation industry.
Traditionally, ensuring compliance with aviation regulations has been a manual and time-consuming process. Maintenance personnel and organizations must meticulously track and document maintenance activities, ensuring that they align with the latest regulations and standards set forth by regulatory authorities such as the Federal Aviation Administration (FAA) and the European Aviation Safety Agency (EASA). However, as regulations continue to evolve and become more complex, manual compliance processes are becoming increasingly inefficient and error-prone.
Regulatory compliance automation offers a solution to these challenges by leveraging technology to streamline compliance processes and ensure adherence to aviation standards seamlessly. By automating routine tasks such as documentation, reporting, and record-keeping, maintenance organizations can reduce the burden on personnel and minimize the risk of errors or oversights. Automated systems can track maintenance activities in real-time, ensuring that they comply with the latest regulations and standards without the need for manual intervention. One of the primary benefits of regulatory compliance automation is the ability to keep pace with evolving regulations and standards effortlessly. As aviation authorities introduce new requirements or update existing regulations, automated systems can adapt accordingly, ensuring that maintenance practices remain in compliance at all times. This proactive approach to compliance minimizes the risk of non-compliance penalties, audits, or enforcement actions, providing organizations with peace of mind and confidence in their regulatory compliance efforts.
Moreover, regulatory compliance automation enables organizations to improve the efficiency and effectiveness of their maintenance operations. By automating routine compliance tasks, maintenance personnel can focus their time and attention on more value-added activities, such as troubleshooting complex issues or implementing preventive maintenance measures. This shift towards automation not only enhances productivity and efficiency but also reduces the risk of human error, ensuring that maintenance activities are conducted with the highest levels of accuracy and precision.
Furthermore, regulatory compliance automation promotes transparency and accountability in aircraft and GSE maintenance. By providing stakeholders with visibility into compliance processes and procedures, automated systems enable organizations to track and monitor compliance efforts in real-time. This transparency fosters a culture of accountability and quality assurance, ensuring that maintenance activities are conducted in accordance with industry best practices and regulatory requirements.
In the realm of aircraft maintenance, regulatory compliance automation is revolutionizing how maintenance activities are planned, executed, and documented. From routine inspections to major overhauls, automated systems can track and record maintenance activities in real-time, ensuring that they comply with the latest regulations and standards. By automating documentation and reporting tasks, maintenance personnel can reduce administrative overhead and focus on the task at hand, ensuring that aircraft are maintained to the highest standards of safety and reliability.
Similarly, in GSE maintenance, regulatory compliance automation is driving efficiency and effectiveness in maintenance operations. From equipment inspections to maintenance tasks, automated systems can track and monitor compliance efforts in real-time, ensuring that GSE is maintained in accordance with regulatory requirements. By automating routine tasks and processes, maintenance organizations can optimize their operations and minimize the risk of non-compliance penalties or enforcement actions.
Despite the numerous benefits of regulatory compliance automation, challenges remain in implementing and adopting these systems effectively. One of the primary obstacles is ensuring that automated systems are robust, reliable, and secure, particularly in environments where safety and security are paramount. Maintenance organizations must invest in robust infrastructure and cybersecurity measures to ensure that automated systems function reliably and securely, minimizing the risk of data breaches or system failures.
In conclusion, regulatory compliance automation is transforming aircraft and GSE maintenance, providing organizations with the tools and capabilities they need to ensure seamless adherence to aviation standards. By automating routine tasks such as documentation, reporting, and record-keeping, automated systems streamline compliance processes and minimize the risk of errors or oversights. While challenges remain, the potential benefits of regulatory compliance automation in aircraft and GSE maintenance are too significant to ignore, making it an indispensable tool for modernizing and optimizing compliance practices in the aviation industry. As organizations continue to embrace automation, the future of maintenance promises to be more efficient, effective, and compliant than ever before.
Conclusion
In the dynamic world of aviation, where safety, reliability, and efficiency are paramount, the future of aircraft and ground support equipment (GSE) maintenance is anything but static. As technology advances and new challenges emerge, there will always be space for continuous innovation in maintenance practices. The aviation industry is inherently adaptive, evolving alongside emerging technologies and addressing new challenges with creativity and ingenuity. In this blog post, we'll explore the concept of continuous innovation in aircraft and GSE maintenance, and how the industry is poised to adapt and evolve in response to emerging technologies and challenges.
The future of aircraft and GSE maintenance is not set in stone. Instead, it is shaped by a myriad of factors, including technological advancements, regulatory changes, and evolving operational requirements. As new technologies such as artificial intelligence (AI), machine learning, and robotics continue to mature, maintenance practices will evolve to incorporate these innovations. From predictive maintenance algorithms that anticipate component failures before they occur to autonomous maintenance vehicles that perform routine tasks with precision and efficiency, the possibilities for innovation are endless.
Moreover, emerging technologies such as blockchain, augmented reality (AR), and additive manufacturing (3D printing) are revolutionizing how maintenance tasks are performed and managed. Blockchain technology, for example, offers a secure and transparent platform for managing maintenance records and tracking the provenance of spare parts, enhancing traceability and accountability in maintenance operations. AR technology, on the other hand, provides maintenance personnel with real-time visualizations and instructions, improving accuracy and efficiency in maintenance tasks. Similarly, 3D printing enables organizations to produce customized spare parts on-demand, reducing lead times and minimizing downtime.
In addition to technological advancements, the aviation industry is also facing new challenges that require innovative solutions. Climate change, for example, is driving the need for more sustainable and environmentally friendly maintenance practices. From electric-powered aircraft to eco-friendly materials and coatings, maintenance organizations are exploring innovative ways to reduce the environmental impact of aviation operations. Similarly, the rise of urban air mobility (UAM) and autonomous aircraft presents new challenges and opportunities for maintenance organizations, requiring them to adapt and evolve their practices to support these emerging technologies.
One of the key drivers of continuous innovation in aircraft and GSE maintenance is the industry's collaborative and forward-thinking culture. Maintenance organizations, manufacturers, regulatory authorities, and technology providers all play a role in driving innovation and pushing the boundaries of what is possible. By sharing knowledge, resources, and best practices, stakeholders can collaborate effectively to develop and implement innovative solutions that address the industry's most pressing challenges.
Furthermore, the pace of innovation in aircraft and GSE maintenance is accelerating, driven by rapid advancements in technology and the increasing demand for more efficient and reliable maintenance practices. Organizations that embrace a culture of innovation and invest in research and development are well-positioned to stay ahead of the curve and maintain a competitive edge in the marketplace. By continuously seeking out new technologies and approaches, these organizations can adapt and evolve in response to changing market dynamics and customer needs.
In the realm of aircraft maintenance, continuous innovation is transforming how maintenance tasks are performed and managed. From advanced diagnostics and prognostics systems to remote monitoring and predictive maintenance algorithms, maintenance organizations are leveraging cutting-edge technologies to optimize their operations and maximize aircraft availability. By embracing innovation, these organizations can reduce costs, minimize downtime, and enhance safety and reliability across their fleets.
Similarly, in GSE maintenance, continuous innovation is driving efficiency and effectiveness in maintenance operations. From automated inspection systems to robotic maintenance vehicles, ground support service providers are exploring innovative ways to streamline their operations and minimize downtime. By embracing new technologies and approaches, these providers can improve productivity, reduce costs, and enhance the overall performance of their GSE fleets.
Despite the numerous benefits of continuous innovation, challenges remain in implementing and adopting innovative solutions effectively. One of the primary obstacles is overcoming resistance to change within organizations, particularly among personnel who may be hesitant to adopt new technologies or approaches. Additionally, addressing concerns about cost, scalability, and compatibility with existing systems is essential to ensure that innovative solutions deliver tangible benefits to organizations and their stakeholders.
In conclusion, the future of aircraft and GSE maintenance is inherently dynamic, shaped by a combination of technological advancements, regulatory changes, and evolving operational requirements. By embracing a culture of continuous innovation, maintenance organizations can adapt and evolve in response to emerging technologies and challenges, staying ahead of the curve and maintaining a competitive edge in the marketplace. While challenges remain, the potential benefits of continuous innovation in aircraft and GSE maintenance are too significant to ignore, making it an indispensable driver of progress and success in the aviation industry. As organizations continue to embrace innovation, the future of maintenance promises to be more efficient, reliable, and sustainable than ever before.
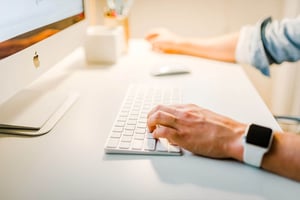