Over 100 professionals participated in the survey, and the following represents their top business challenges that year, as also posted on AviationPros.com:
Source: https://www.aviationpros.com/
As a response to these recent findings, we recently held a webinar to present our point of view on developing approaches to overcome some of these challenges within our GSE Optimization Framework.
First, a few thoughts on the top few challenges.
Finding and Retaining Staff
One of the top challenges in the aviation industry is finding and retaining staff. This is true across various areas of the industry, including ground support services. In the Ground Support Worldwide magazine survey, this concern was ranked as the number one challenge by over 40% of respondents.
The aviation industry is facing a shortage of skilled workers, particularly mechanics and pilots. This means that companies are having more difficulty filling open positions and retaining current employees. This challenge is compounded by the fact that other industries, such as healthcare and technology, are also competing for talented workers. This creates a dilemma for aviation companies: how to attract and retain the best employees without outbidding themselves in the job market.
With COVID-19, many senior technicians have retired, and the younger generation, used to modern technology, are more often expecting easy-to-use systems that are intuitive and easy to come up to speed on. The Facebook generation is computer literate, and when they're hired, they expect you to have a system that's easy to use and helps them conduct their work. One way to overcome the knowledge gap between senior and junior employees is by providing younger employees with OEM manuals or recorded videos at their fingertips to show them how to best handle their work. This can be invaluable for the new generation of workers who may feel overwhelmed by the huge amounts of data they're expected to absorb.
Acquiring or Maintaining Equipment
Acquiring or maintaining GSE equipment is another significant challenge that GSE professionals face. The business outcome of GSE availability and reliability is crucial. It's essential to make sure that your current assets are reliable, and as you go to look for new equipment, you can justify the business case to do that. One way to achieve this is by having a system in place to track your equipment and its maintenance schedule. This can help you identify potential issues before they happen and ensure that your equipment is always in top condition. Another solution is to invest in best-of-breed software that can help you manage your assets, track repairs and maintenance, and plan for equipment replacement. With the right tools in place, you can ensure the reliability and availability of your GSE equipment and minimize potential downtime.
Complying with Industry Regulations
Another significant challenge for aviation companies is complying with industry regulations. The aviation industry is heavily-regulated, and companies must meet strict standards for safety, security, and environmental impact. These regulations are necessary to maintain the industry's reputation for safety and reliability, but they also create additional costs and administrative burdens for companies.
Furthermore, regulations are subject to change and updates, which means that companies must constantly stay informed and up-to-date. This creates an ongoing challenge for companies to ensure that they are meeting all requirements, particularly as new regulations are introduced. Nonetheless, maintaining compliance is essential for aviation companies to remain operational and avoid costly fines or sanctions.
The GSE Optimization Framework
At the heart of overcoming this list of challenges, ultimately, lies the need to drive better business outcomes. But, in order to drive those outcomes, we believe requires an intentional focus on standardizing the right data, enriching that data with context, uncovering useful insights and taking the right set of actions. While seemingly simple, doing it correctly can be difficult.
Data Standardization
Standardizing GSE data is a crucial step towards optimizing maintenance and workflow management processes. By using standard naming conventions and cleaning data, organizations can avoid the classic “garbage in, garbage out” problem. This enhances visibility and generates reports that are specific and relevant to the organization. Furthermore, standardizing data can help achieve better supply chain process for parts and components.
Context is Everything
Context enriches data and helps provide a clearer picture of the story behind the pieces. In GSE maintenance, work is often nonlinear and dynamic, making it vital to have rich context. By linking different work streams and using smart workflows and integrations, organizations can understand the entire workflow and make informed decisions. Well-defined workflows and accurate data are critical to obtaining insights to drive full efficiencies.
Useful Insights
Generating insights is about asking the right questions and collecting and preparing data for analysis. Not all data available is relevant for the questions asked by teams. Organizations must slice and dice the data, utilizing dashboards that are specific use cases to GSE. By doing so, they can obtain insights and take informed actions.
Taking Action
Of all the steps, taking the right action is perhaps the most important. Insights alone will not lead to positive results; teams must act on those insights to drive outcomes. Organizing the data, aligning culture and technology, and using data to inform decisions should be the primary focus. Doing so will help organizations streamline repeatable processes across the team and drive full efficiencies.
Why Domain Expertise Matters in GSE?
When it comes to delivering recommendations and insights in the aviation industry, domain expertise plays a crucial role. While insights on their own can be helpful, recommendations on what actions to take are even more valuable. That's where working with a solution provider that has specific GSE domain expertise can be beneficial. Having a partner with a broad perspective and understanding of the industry can help you achieve your business outcomes faster.
The Value of Benchmarking
Benchmarking is a critical element for achieving business outcomes in the aviation industry. With the help of a solution provider with domain expertise, benchmarking can allow you to gain insight into what other companies are doing in aviation and what the industry recommends. This information can be helpful in making informed decisions on what actions to take. At EBIS, we have specific GSE domain expertise and have worked with various organizations, providing us with unique insights that we can use to deliver value-based recommendations. By combining GSE data with smart workflows and integrations, we can help you uncover insights and deliver recommendations that align with your business outcomes.
A Brief Look at EBIS for GSE Asset Management
EBIS, a best-of-breed solution for the GSE industry, optimizes ground support equipment maintenance. With its dynamic update feature, both technicians and parts are monitored in real-time, which allows companies to view the total spend of all their GSE assets. The software allows for precise tracking of specific details, such as parts, components, asset type, part type, and location. EBIS can integrate with all telemetry vendors' data through an open API, which provides telemetry data such as position, usage, meter readings, and fluid levels. This data can be used later when trying to include those pieces of equipment in the maintenance process.
EBIS provides detailed reports that show how motorized versus non-motorized assets are performing, which assets are out of service, and how technicians are performing. Companies can focus and drill down on specific areas for detailed analysis, such as looking at specific equipment types such as bag tugs. The onboarding process takes between four to seven weeks, and the software can train a technician in 45 minutes. EBIS provides a dedicated Customer Success Manager who has lots of experience in the aviation business. Further support is provided by our team of aviation experts, such as our Director of Customer Impact, who has been in the aviation business for 25 years. Business reviews can be set up based on the company's preferences.
One example of how EBIS has helped drive better performance in GSE maintenance is with a global aviation service provider who had been primarily conducting reactive maintenance. Their work order on-time performance was only 42 percent in 2018, and 70 percent of all their work orders were unscheduled with no supply chain integration. After implementing EBIS, they improved their work order on-time performance to 90 percent and decreased their unscheduled work orders to 34 percent. The software streamlined their supply chain and provided the insights they needed to make data-driven decisions to optimize their GSE maintenance.
Improving Maintenance Efficiency with Proactive Maintenance
In order to achieve a more efficient maintenance process, it is important to focus on proactive maintenance practices. This means identifying and addressing potential issues before they become actual problems. By taking this approach, you can save time, money, and improve overall performance.
One way to achieve this is by streamlining your maintenance process. This can include improving your data management practices, establishing naming conventions, and promoting user adoption of your maintenance system. By having consistent and accurate data, you can better align your work orders with your parts purchasing, leading to a more efficient process.
Another element of proactive maintenance is scheduling regular preventative maintenance checks for your equipment. By doing so, you can identify potential issues and make necessary repairs before they lead to more costly breakdowns. This helps to reduce the number of unscheduled maintenance checks, which results in faster repair times and ultimately, improved performance.
Implementing a proactive maintenance approach may require some initial effort and focus, but the benefits of doing so can be significant in the long term. By identifying underperforming assets and implementing QC checks, you can improve on-time performance and reduce unscheduled maintenance checks. With streamlined processes and regular preventative maintenance, you can ensure that your equipment is reliable and available, reducing the risk of downtime and costly repairs.
Improving On-Time Performance through Detailed Reporting
Detailed reporting can help you identify areas where you can reduce costs and improve performance. With detailed reports, you can track scheduled and unscheduled maintenance, and identify areas where you can improve on-time performance. By doing so, you can reduce unscheduled downtime failures and eliminate firefighting.
For instance, reports can highlight unscheduled PMs completed before scheduled PMs, as well as the number of unscheduled PMs completed after PM checks. This information can help you identify training issues among your technicians, and improve your ability to plan for parts. By measuring on-time performance, you can reduce unscheduled work, which results in costly repairs.
Reducing Unscheduled Maintenance through Parts Integration
Integrating parts into your maintenance operations can streamline your supply chain and reduce the risk of unscheduled maintenance. With parts integration, you can see part numbers, descriptions, quantities, and prices. You can also get an estimate of when these parts will be delivered.
This information can be particularly useful if you hold stock, purchase from a third party vendor, or use a service like Sage or Napa. Reports can give you the ability to issue purchase orders to third parties, bill vendors for parts, and reduce parts from your stock.
At EBIS, we're constantly innovating to meet the needs of our customers. We support a range of industries, including commercial and cargo airlines, grand handlers, fueling companies, leasing companies, and refurbished companies. Our new service request capability provides updates on out-of-service equipment and can help you improve the efficiency of your operations.
Equipment Maintenance and Tracking
One of the top challenges for businesses is maintaining and purchasing new equipment. This is where dynamic dashboards come in handy. With EBIS' dynamic dashboards, you can track and maintain equipment with ease. The dashboard allows you to view the total number of equipment you have over a certain period, the number of work orders you've opened, and your total spend broken down by labor and part spend.
Drilling Down into Equipment Data
The beauty of EBIS' dynamic dashboards is that you can also drill down further into the data. You can view the equipment manufactured in a specific year, the work orders opened, and the cost of labor and parts. You can also drill down into specific equipment components and parts. This information helps you figure out how well your equipment is working and which components and parts are costing you the most money. With this information, you can make informed decisions on when and how to service your equipment. EBIS' dynamic dashboards make equipment maintenance and tracking a streamlined process for your business.
Understanding EBIS Capabilities and Costs
When it comes to determining the capabilities and costs of a potential software solution, it's important to first identify the specific requirements of your organization. EBIS can offer a range of solutions that vary in price and functionality, and it's crucial to understand which option best suits your needs.
Costs will depend on factors such as the number of assets you have - motorized and non-motorized - as well as the specific capabilities you require. EBIS typically comes in three versions: core, advanced, and professional. It's important to understand the differences between each option and what features you need for your organization. Before determining costs, have a conversation with an EBIS provider to identify your requirements and which version of EBIS would be best suited for your organization's goals.
Overall, understanding the capabilities and costs of EBIS requires an analysis of your organization's specific needs. Reach out to an EBIS provider for a conversation on which version would be best suited for your organization and its goals. Don't be shy to ask questions and engage further to ensure your EBIS investment delivers the desired outcomes.
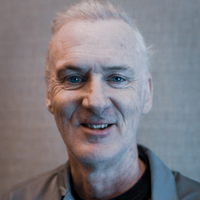
COMMENTS