In 2024, many aircraft maintenance repair facilities faced a dual challenge: how to improve profitability while navigating constraints in technician availability. By focusing on capacity improvements and operational efficiency, facilities can achieve higher job volumes, better resource allocation, and ultimately, increased profitability. The visual framework provided above breaks down the levers repair facilities can adjust to optimize their performance.
The Profitability Equation
Profitability in repair stations hinges on the balance between revenue and costs. Revenue is driven by job volume and job size, while costs are shaped by labor, inventory, and other variable inputs. The key to improving profitability is optimizing job volume through enhanced technician capacity and process efficiency.
Lever 1: Expanding Technician Capacity for Higher Job Volume
Technician Utilization Rate
The foundation of job volume is maximizing the technician utilization rate. This metric evaluates how effectively available technician hours are being allocated to meaningful work. Improving utilization requires:
- Better scheduling and planning tools: Ensuring technicians spend less time waiting and more time fixing.
- Reducing rework through training: Bolstering the first-time fix rate (FTFR) minimizes inefficiencies and maximizes available hours.
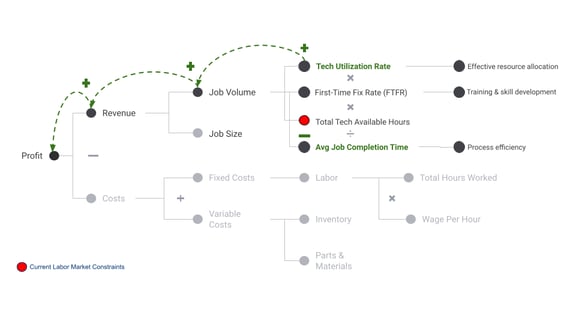
Navigating Labor Market Constraints
In today’s tight labor market, technician shortages are a reality. Addressing these constraints requires innovative solutions:
- Upskilling existing technicians to handle more complex tasks efficiently.
- Streamlining less technical work by leveraging technology or outsourcing non-core tasks.
Average Job Completion Time
Reducing the average time it takes to complete a job increases the facility’s throughput. Workflow optimization and improved access to parts and materials can have a direct impact on job completion rates, boosting overall capacity.
Streamlining Workflows
One of the primary drivers of delays is inefficiency in workflows. Streamlining processes ensures that every step in the maintenance or repair cycle adds value without unnecessary delays. Consider these strategies:
- Standardizing Procedures: Developing step-by-step task guides or templates can reduce the time spent figuring out the next steps. This is particularly helpful for repeatable jobs like inspections or part replacements.
- Optimizing Task Sequencing: Ensuring technicians have a clear roadmap of what to do and in what order minimizes downtime and confusion.
- Digitizing Task Management: Utilizing software to track progress in real time helps supervisors identify bottlenecks and intervene before delays occur.
Improving Parts and Materials Access
The availability of parts and materials plays a significant role in job completion time. Delays often arise when technicians must pause their work to wait for the right tools or components. Solutions include:
- Stocking Smart Inventory: Maintaining an inventory of high-demand parts reduces waiting time. Historical data can help identify which items are critical to keep on hand.
- On-Demand Ordering Systems: Partnering with suppliers that offer fast turnaround times for less common parts ensures availability without overstocking.
- Streamlined Parts Pickup: Reducing the time it takes for technicians to retrieve parts can make a surprising difference. For example, strategically placing parts stations closer to work areas saves significant time over the course of a day.
Leveraging Technology for Efficiency
Technology solutions can significantly reduce average job completion time by automating repetitive tasks and reducing manual errors. Key examples include:
- Digital Documentation: Eliminating paper-based systems reduces time spent searching for information. Technicians can access schematics, service bulletins, and manuals with just a few clicks.
- Mobile Tools: Equipping technicians with mobile devices allows them to log work, track progress, and request parts without leaving their workstations.
- Predictive Analytics: Data-driven insights can forecast potential delays, enabling managers to adjust workflows or inventory levels proactively.
Enhancing Technician Productivity
Technician productivity is directly tied to job completion time. Some strategies to improve productivity include:
- Cross-Training Technicians: Training technicians to handle a wider variety of tasks ensures that jobs aren’t delayed while waiting for a specialist.
- Reducing Non-Value-Added Work: Analyzing how technicians spend their time can reveal opportunities to eliminate unnecessary steps, such as excessive administrative tasks.
- Reducing Rework: Improving the First-Time Fix Rate (FTFR) ensures technicians don’t need to revisit the same job multiple times, saving hours of work.
Monitoring and Continuous Improvement
Reducing average job completion time is not a one-and-done effort—it requires ongoing monitoring and adjustment. Repair facilities can:
- Track Metrics in Real Time: Regularly measure job completion times to identify patterns and outliers.
- Conduct Post-Job Reviews: Assess completed jobs to identify inefficiencies and areas for improvement.
- Incorporate Feedback: Technicians often have firsthand insights into what slows them down. Incorporating their feedback can lead to meaningful improvements.
Lever 2: Driving Revenue Growth Through Sales Efficiency
Sales teams play a critical role in ensuring repair stations maintain a steady pipeline of projects. Efficiency improvements in this area complement operational changes on the floor:
- Shortening the sales cycle: Faster response times and better communication with potential clients enable quicker job onboarding.
- Leveraging digital sales tools: Automating quote generation and customer follow-ups allow the sales team to focus on building relationships and closing deals.
When sales and operational efficiencies align, repair facilities can increase the number of jobs they take on, driving significant revenue growth.
The Ripple Effect of Efficiency Gains
Enhancements in technician capacity and sales team performance create a ripple effect across the repair facility:
- Increased Job Volume: More jobs completed on time translate directly to higher revenue.
- Improved Cost Control: Efficient resource use reduces variable costs like overtime and inventory waste.
- Scalable Growth: By resolving bottlenecks, facilities position themselves to handle more work without significantly increasing fixed costs.
Realizing Profitability Gains in 2025
Aircraft maintenance repair facilities that focus on technician utilization, first-time fix rates, and sales efficiencies will position themselves for sustainable growth in 2025. By aligning these strategies, repair stations can turn operational improvements into measurable profitability increases, even in the face of labor market constraints.
The journey toward profitability begins with actionable insights and the commitment to continuous improvement. How will your repair station rise to the challenge?
COMMENTS