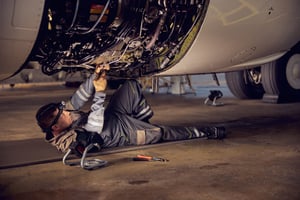
Efficient Work & Repair Order Management
Work order management lies at the heart of maintaining aircraft reliability and compliance. EBIS helps you facilitate the seamless orchestration of routine inspections, scheduled maintenance tasks, preventive measures and more.
Streamline techs' tasks with minimal training and simple workflows.
Make it simple for technicians to enter data, track time and more with an easy-to-use mobile interface.
- Easily view how technicians spend their day and use this data to help ensure proper training and data entry.
- Enable technicians to work remotely and in real-time with all necessary information at their fingertips.
- Stored corrective actions
- Take photos and videos of equipment and parts and view equipment manuals and memos.
-
Easily navigate and oversee the linked components, inventory, and associated resources.
Key Features
Related Posts
How Clemens Aviation Scaled from a Small Team to 130 Employees
Navigating Aviation Challenges in Hawaii: Insights from PMX Aviation
Improving Technician Workflows with Digital Tools and Standardization
Case Studies
Streamlining Growth and Maintenance Excellence at Apex Aviation
Elevating Maintenance Operations At Appalachian Aero Group
Optimizing Fleet Management and Operations at CharterJet Solutions
Frequently Asked Questions
-
Enhanced Organization: The repair order feature provides a centralized platform for managing and organizing maintenance tasks. It allows maintenance teams to systematically document and track each repair or service request, ensuring a clear and structured workflow.
-
Efficient Communication: By utilizing a repair order system, communication between maintenance personnel, engineers, and relevant stakeholders is greatly improved. Real-time updates and notifications ensure that everyone involved is informed of the status of a repair, facilitating quicker decision-making and collaboration.
-
Detailed Documentation: Maintenance crews can create detailed records for each repair order, including information on the nature of the issue, the steps taken for resolution, and any parts or components replaced. This documentation is valuable for regulatory compliance, historical analysis, and future maintenance planning.
-
Optimized Resource Management: The repair order feature assists in efficient allocation of resources such as manpower, tools, and spare parts. Maintenance teams can prioritize tasks based on urgency and criticality, reducing downtime and improving overall operational efficiency.
-
Compliance and Auditing: For aviation authorities and regulatory compliance, having a comprehensive repair order system is essential. It enables organizations to maintain meticulous records of maintenance activities, facilitating audits and ensuring adherence to safety and regulatory standards.
-
Cost Control: With detailed records and insights into maintenance activities, organizations can better manage costs associated with repairs and maintenance. Analyzing trends and historical data allows for more accurate budgeting and cost forecasting.
-
Performance Analysis: The repair order feature enables the tracking of maintenance trends and recurring issues. This data is invaluable for conducting performance analysis, identifying patterns, and implementing preventive measures to minimize future maintenance issues.
-
Fleet Management: For organizations with multiple aircraft, the repair order feature aids in comprehensive fleet management. It provides a holistic view of the maintenance status of each aircraft, enabling better decision-making for fleet deployment and scheduling.
-
Increased Aircraft Availability: By streamlining maintenance processes and minimizing downtime, the repair order feature contributes to increased aircraft availability. This is critical for meeting operational demands and maintaining a high level of service reliability.
-
Customer Satisfaction: Ultimately, efficient maintenance practices supported by a robust repair order system contribute to overall customer satisfaction. Reliable aircraft performance and timely maintenance lead to fewer disruptions, enhancing the reputation of the airline or aviation service provider.
The repair order feature in an aircraft maintenance management solution serves as a versatile tool, addressing various critical use cases within the realm of aviation maintenance. Here are some typical use cases:
-
Scheduled Maintenance: Aircraft undergo routine maintenance checks at specified intervals. The repair order feature helps schedule and manage these planned maintenance activities, ensuring that each task is systematically documented, executed, and recorded.
-
Unscheduled Repairs: In the event of unexpected issues or malfunctions, the repair order feature facilitates the swift initiation and tracking of unscheduled repairs. Maintenance teams can quickly document the problem, assess the required actions, and communicate effectively to address the issue promptly.
-
Component Replacement: When aircraft components or parts need replacement due to wear and tear, the repair order system ensures a systematic approach. It tracks the replacement process, documents the details of the new components, and helps maintain an accurate inventory of spare parts.
-
Inspections and Checks: Regular inspections, including pre-flight and post-flight checks, are integral to aviation safety. The repair order feature assists in planning, conducting, and documenting these inspections, providing a comprehensive overview of the aircraft's condition and compliance with safety standards.
-
Avionics Upgrades: Upgrading avionics systems is a common practice to enhance aircraft capabilities. The repair order feature aids in planning and executing avionics upgrades, ensuring that the process is well-documented and that any necessary regulatory approvals are obtained.
-
Troubleshooting and Diagnostics: When technical issues arise, the repair order system supports maintenance teams in troubleshooting and diagnostics. It allows technicians to log their findings, track the steps taken to identify and rectify problems, and maintain a comprehensive history for future reference.
-
Regulatory Compliance: Compliance with aviation regulations is paramount. The repair order feature helps organizations adhere to regulatory requirements by documenting each maintenance activity in detail. This documentation is crucial for audits and inspections conducted by aviation authorities.
-
Warranty Tracking: Many aircraft components come with warranties. The repair order system helps in tracking warranty information for each part, ensuring that repairs and replacements are performed within the warranty period to maximize cost savings.
-
Historical Data Analysis: The repair order feature stores a wealth of historical data related to maintenance activities. This information is valuable for analyzing trends, identifying recurring issues, and implementing preventive measures to enhance overall aircraft reliability and performance.
-
Communication and Collaboration: Effective communication among maintenance teams, engineers, and other stakeholders is vital. The repair order system facilitates collaboration by providing a centralized platform for communication, allowing real-time updates, and ensuring that everyone involved is informed about the status of ongoing repairs.
-
Resource Allocation: Optimizing the use of resources such as manpower, tools, and spare parts is a key aspect of aircraft maintenance. The repair order feature helps in planning and allocating resources efficiently, reducing downtime and enhancing operational efficiency.
In summary, the repair order feature in an aircraft maintenance management solution addresses a wide range of use cases, contributing to the systematic planning, execution, and documentation of maintenance activities while ensuring compliance with industry standards and regulations.
The Problem
As an aviation services provider that needs to ensure the efficient and compliant maintenance of aircraft, you face the challenge of managing all the data required to do so, including work & repair orders, inventory, parts, tools, aircraft, warranties, labor hours, etc.
But, in order to optimize and scale your operation effectively, reduce risk, improve margins and drive efficiency, you may be using a solution that is difficult-to-use, cost-prohibitive, feature deficient or not appropriately designed to meet your needs throughout the maintenance lifecycle.
The Solution
As an aviation services provider that needs to ensure the efficient and compliant maintenance of aircraft, you face the challenge of managing all the data required to do so, including work & repair orders, inventory, parts, tools, aircraft, warranties, labor hours, etc.
But, in order to optimize and scale your operation effectively, reduce risk, improve margins and drive efficiency, you may be using a solution that is difficult-to-use, cost-prohibitive, feature deficient or not appropriately designed to meet your needs throughout the maintenance lifecycle.
SECTION STEPS - TITLE
Description. Lorem ipsum dolor sit amet, consetetur sadipscing elitr, sed diam nonumy eirmod tempor invidunt ut labore et
Activities
Inspections
Task Imports / Integrations
CHALLENGES
Inefficient inspection process
Double entry from other systems
Tools & Inventory
Purchase Orders
Parts Management
Vendor Management
Workflow Visibility
Certification Tracking
Compliance Data
Log Books
Billing & Invoicing
Accounting
Schedule a 30-Minute Demo
Discover the power of EBIS 5 Repair Station Management Software with our 30-minute demo. Let us guide you through all the features and benefits of this industry-leading tool, and learn how to run your Repair Station more efficiently than ever before. Join us now and unlock the full potential of EBIS!
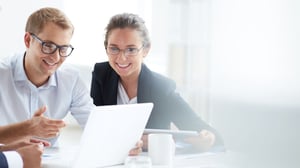
SERVICE VIDEO
Showcase your awesome service with quality video content.
Lorem ipsum dolor sit amet, consetetur sadipscing elitr, sed diam nonumy
27K | 1.2MIO |
Lorem ipsum dolor sit amet, consetetur sadipscing elitr, sed diam sit amet, consetetur elitr. | Lorem ipsum dolor sit amet, consetetur sadipscing elitr, sed diam sit amet, consetetur elitr. |